Strategic maintenance planning is critical to optimizing machine functionality and minimizing unexpected downtime. That means employing a mix of four primary maintenance strategies: Reactive maintenance, which involves taking [...]
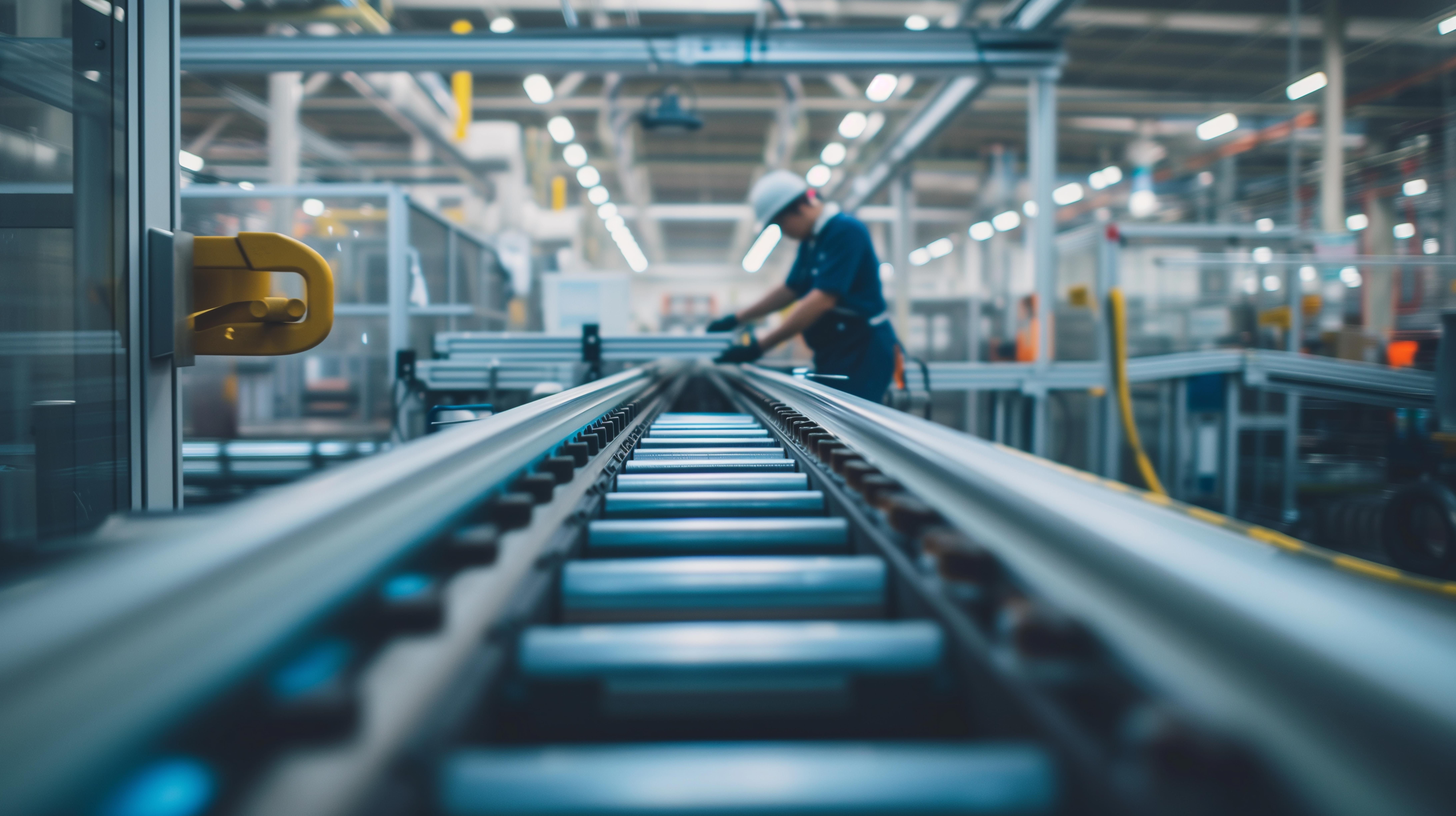
Strategic maintenance planning is critical to optimizing machine functionality and minimizing unexpected downtime. That means employing a mix of four primary maintenance strategies: Reactive maintenance, which involves taking action after a breakdown occurs; Preventive maintenance, which involves regular checks to prevent problems; Predictive maintenance, which uses data to anticipate and address problems before they occur; and Predetermined maintenance, which is based on external recommendations or standards. Each strategy provides a unique approach to maintaining operational efficiency and reducing the risk of unplanned downtime depending on the value of the machine and the cost of downtime.
The core maintenance strategies – reactive, preventive, predictive, and planned – are well established. Yet innovative modifications of these methods have evolved to better meet specific operational needs. These advanced approaches address the unique requirements of various industries to ensure that maintenance planning is not only proactive but also highly effective. Organizations can leverage these strategies to significantly improve their maintenance operations, resulting in greater reliability and performance.
In certain sectors, for example, fitness centers, a reactive maintenance approach may be more practical, given the long life of commercial fitness equipment and members’ tolerance for occasional equipment unavailability. On the other hand, in manufacturing, machines often have predictable failure patterns that engineers are familiar with after years of observation.
That allows seasoned engineers to develop an intuitive sense of upcoming breakdowns, but depending solely on intuition still carries the risk of unexpected downtime when things go wrong. This can prove to be pretty expensive for manufacturers, with downtime costs ranging from $39,000 to over $2 million depending on the industry, which further demonstrates the importance of a strategic, informed approach to maintenance planning.
1. Reactive maintenance: if it breaks, I will fix it
Companies often default to a reactive approach when they overlook the importance of planned maintenance strategies (or equipment has such a low value that it can be easily replaced). This typically means that maintenance tasks are triggered by a machine breakdown or when the inefficiency of the machine becomes so disruptive that maintenance is the only option. This strategy is also commonly referred to as run-to-failure maintenance and involves running equipment until it fails. Smaller companies are also more likely to follow this path due to limited resources or maintenance expertise.
Corrective maintenance also often falls into the category of a reactive maintenance strategy because maintenance is only performed after an abnormality has been detected and an action is taken to return a machine to standard operating condition. As with most reactive maintenance strategies, this approach is typically used when the cost of downtime or repairing a machine is less than the cost of scheduled maintenance.
For business owners, especially in smaller environments, unexpected repairs often require dipping into savings to hire outside professionals to fix the problem. Larger companies have the option of issuing internal work orders after a problem occurs. However, forward-thinking SMBs and enterprises alike understand the high costs associated with lost production time when it comes to critical equipment — not only in direct expenses but also in meeting payroll and order commitments during downtime.
Typically, when the cumulative cost of equipment failure begins to exceed the investment in a planned maintenance strategy, a transition toward proactive maintenance strategies is required. Assessing the readiness for such a shift involves a thorough analysis of equipment performance, repair frequency, and the financial costs of production downtime. If the cost analysis points to proactive maintenance, it’s time for companies to explore appropriate strategies that meet their operational needs. Please also note that this strategy will also depend on the type of equipment as well.
When does reactive maintenance make sense?
Reactive maintenance may be the best choice when you have assets that are (1) impossible to maintain, (2) less expensive to buy than to maintain, (3) easy to replace, or (4) not important for critical operations. For example, replacing faulty smoke detectors may be more efficient than repairing them, unlike plumbing systems where regular maintenance can prevent costly repairs.
What are the downsides of reactive maintenance?
While reactive maintenance is sometimes appropriate, it has significant drawbacks. These include an increased risk of sudden failures that result in downtime, reduced asset life due to maintenance neglect, and the need for readily available personnel and spare parts to address unforeseen breakdowns. Before deciding on a reactive maintenance model as the preferred strategy, these factors have to be carefully weighed against the potential savings in personnel and materials.
2. Preventative maintenance: I will fix it before it breaks
Preventive maintenance is often a cost-effective strategy to extend equipment life and minimize the risk of downtime. This approach proactively addresses equipment failure and significantly reduces the likelihood of subsequent equipment breakdowns that could place undue stress on other components if the machine is allowed to run-to-failure. While manufacturers generally mix maintenance strategy plans depending on the machine, a 2021 study from Plant Engineering found that 88% of industrial facilities follow a preventive maintenance strategy while 52% have a computerized maintenance management system (CMMS) and 51% use a run-to-failure or reactive method. Generally, preventive maintenance follows a recommended schedule, ensuring that equipment is serviced in scheduled maintenance intervals.
Despite the benefits, preventive maintenance isn’t without its challenges. It sometimes requires replacing parts that appear to be in perfect working order to meet a predetermined maintenance schedule. This practice can lead to increased costs, especially for parts that are hard to find or nearing obsolescence. As a result, many companies prioritize preventive maintenance for critical assets where unexpected downtime could result in significant operational and financial setbacks but is not costly enough to justify the investment in predictive maintenance software.
When does preventative maintenance make sense?
Preventive maintenance is most beneficial for equipment that, if it fails, could significantly disrupt production or operations. The strategy is cost-effective when the cost of preventive or corrective actions are less expensive than the potential cost of failure. That’s why, for less critical or easily replaceable machines, a reactive maintenance approach may be more practical.
A comprehensive preventive maintenance plan considers the entire lifecycle of an asset, including recurring problems. Initially, a new machine should follow the manufacturer’s maintenance guidelines (predetermined maintenance). Over time, experienced technicians can begin to identify patterns that help predict future failures, allowing for a transition to a more personalized preventive maintenance schedule. This custom approach allows maintenance frequencies to be set based on expert knowledge, optimizing the timing of interventions to align with planned downtime, thus minimizing the impact on production. The scope of maintenance can range from simple adjustments and lubrication to major repairs and parts replacements, all scheduled to ensure minimal disruption to operations.
What are the downsides of preventative maintenance?
While there are benefits to preventive maintenance, it’s important to be aware of its potential drawbacks. For example, inefficiencies can result from spending too much time on non-critical maintenance tasks or from misdirected efforts that inadvertently damage the machine, causing unplanned downtime. If maintenance is not performed on time, the machine might find itself in a run-to-failure situation.
3. Predictive maintenance: I know when it will break, so I fix it before
Predictive maintenance, also known as reliability-centered maintenance (RCM), has emerged alongside the Internet of Things (IoT), which enabled machines and computer systems to be wirelessly connected via the internet. This development facilitated the use of algorithms to analyze data and predict potential failures before they happen. For example, the association of certain temperature patterns with machine breakdowns could signal an upcoming breakdown, and additional data points such as vibration, pressure changes or noise levels can be used to further refine the predictive capabilities.
The main advantage of predictive maintenance is its data-driven approach, which eliminates reliance on gut feeling or generic manufacturer guidelines. For equipment with infrequent maintenance needs, the lack of technical experience can hinder the ability to intuitively predict failures, making the data-driven recommendations provided by predictive maintenance tools invaluable. By relying on alerts from predictive tools to guide maintenance actions, this strategy enables maintenance teams to prioritize critical tasks and optimize operational efficiency.
When does predictive maintenance make sense?
Predictive maintenance is particularly well suited to high-value assets that are expected to have a long operating life, where the initial investment in advanced technology can be justified by a longer, more efficient service life. It’s generally used for mid-value assets that are critical to manufacturing processes, where unexpected downtime can result in significant financial losses.
The selection of predictive maintenance software requires careful consideration of how its condition monitoring capabilities can proactively suggest maintenance actions to prevent equipment failures.
What are the downsides of predictive maintenance?
Although the predictive maintenance market rose by 11% from 2021 until 2022, most tools still have an accuracy rate that’s lower than 50% due to the infancy of the technology. The up-front costs associated with acquiring and integrating new technologies and software are a significant barrier to the adoption of predictive maintenance. That’s why when the decision is made to invest in these technologies, it’s important that these tools fit into the daily routines and operational practices of maintenance teams. The team’s willingness and ability to use predictive maintenance tools effectively determines their effectiveness, meaning that a tool with a smoother user interface might be a better option.
To determine if predictive maintenance software is a good fit for the needs of your organization, you should conduct a comprehensive review of your existing maintenance procedures. Engage maintenance team members to assess how predictive maintenance tools could improve their workflow and identify the most beneficial features. Getting early buy-in from the operations team can help align maintenance strategies with broader business goals. This will create a more receptive environment for the technological transition that predictive maintenance software entails.
This collaborative approach to predictive maintenance reinforces the importance of strategic integration and operational alignment to realize the full benefits of advanced maintenance technologies. It also ensures that your organization is well-positioned to improve asset reliability and operational efficiency.
4. Predetermined maintenance: Manuals tell me when to fix it
Predetermined maintenance, also known as manufacturer-recommended maintenance, is a strategy where maintenance intervals and tasks are outlined by those who designed and built the machine. This approach often includes guidelines for regular inspections, maintenance, and deep cleaning, as outlined in maintenance manuals. If we take the example of small appliances, we can often see consumer-focused versions of this for espresso machines and vacuum robots that explain how maintenance can be scheduled to improve the lifetime of the machine.
Predetermined maintenance is especially useful for new equipment. Following the manufacturer’s guidelines provides a solid foundation for maintenance planning when engineers and maintenance teams are not fully familiar with the specifics of a new machine. This strategy serves as a stepping stone to more customized maintenance approaches, such as reactive, preventive or predictive, depending on changing organizational needs and machine performance.
When does predetermined maintenance make sense?
The biggest advantage of this strategy is the confidence in the maintenance plan that is created by the manufacturers, who have a complete understanding of the equipment. For new machines that haven’t collected enough historical data or experience from the maintenance team, this is the best approach before transitioning to something more exact.
Predetermined maintenance manuals often use historical data and performance metrics to create maintenance schedules that ideally extend the life of the equipment and maintain its efficiency.
This strategy is often recommended for equipment that comes with specific manufacturer recommendations and often impacts new machines that range from moderately valuable to high-value assets that are critical to production processes. The structured nature of predetermined maintenance plans provides a more systematic approach compared to the unpredictability of reactive, or run-to-failure, maintenance.
What are the downsides of predetermined maintenance?
However, the one-size-fits-all nature of manufacturer-provided schedules may not be perfectly suited to every operational context. This can lead to over-maintenance or under-maintenance. Over-maintenance can result in the unnecessary replacement of still-functioning parts, while under-maintenance can leave equipment vulnerable to unexpected failures. In addition, external factors such as environmental conditions may require adjustments to predetermined maintenance schedules to better suit local conditions, which can vary significantly from one location to another.
If we look at a factory in Venezuela and one in Finland, we can already see that the weather and humidity are going to be very different. This could have a major impact on the overall condition of the machine —which in turn would require a different maintenance schedule.
Rethinking traditional maintenance strategies with Elara
If businesses fail to approach maintenance tasks strategically, they are likely to be stuck in a reactive maintenance cycle or a continuous state of emergency. For teams, having to fight fires on a daily basis is incredibly inefficient and exhausting. That’s why most companies are adopting proactive maintenance strategies. However, moving from a run-to-failure approach to a more proactive one requires a major shift in mindset. The entire organization needs to be ready to take on new responsibilities that don’t fit with how they’re used to working.
It’s also not uncommon for maintenance teams to become disorganized when maintenance strategies change. Constant planning, scheduling and tracking must become a meticulously planned system that often goes against human intuition. This becomes even more difficult when the team is four or more people. Or when a company has too many machines that need proactive maintenance.
This is where a maintenance management software solution can help. Without adding additional communication channels, maintenance software can track, schedule, and assign maintenance tasks to the appropriate team members. Team collaboration, usability, and cloud connectivity are key features you should consider. The right software can be a game changer for team efficiency as well as performance.
Software enables the communication and understanding maintenance and production teams need to achieve their common goal: machine uptime. Ideally, planned maintenance should be coordinated about four weeks in advance, which often results in reactive maintenance similar to I see it’s broken, can you fix it? Without a clear problem, production teams unfortunately often view maintenance teams as a disruption to their other objectives and deadlines.
Maintenance software can provide critical support by facilitating this work and providing a clear path for everyone to follow. This ensures that no maintenance action is left uncommunicated. For maintenance teams, this means they can perform preventive and predictive maintenance without worrying about impacting production. As a result, both teams are guided to a more harmonious working environment that benefits the teams, the company and the machines, while increasing productivity and efficiency in the long term.
At Elara, we’re helping organizations optimize their long-term maintenance processes. Without disrupting existing workflows, our solution enables teams to change their mindset from reactive to proactive. Elara does this by unlocking the potential for cross-departmental collaboration through an unlimited number of users and data storage.
Our customers, including those in the intralogistics sector, have used Elara to implement preventive and predictive maintenance strategies in their companies. Not only have they made their maintenance processes more efficient, but they’ve saved significant costs by avoiding costly repairs.
See how the Head of Maintenance of EUROQUARZ GmbH, a German quartz mining and processing enterprise, describes the benefits of using Elara.
[In the age of AI, you never know if you’re reading something copy and pasted directly from ChatGPT, or if an actual human sat down to write this with some cool facts from their boss or operations team. That’s why we created a short and simple introduction to how we create content at Elara.]