Thanks to Elara, we now have seamless access to machine history and maintenance reports. Being able to view object information and nameplates directly on site saves us valuable [...]
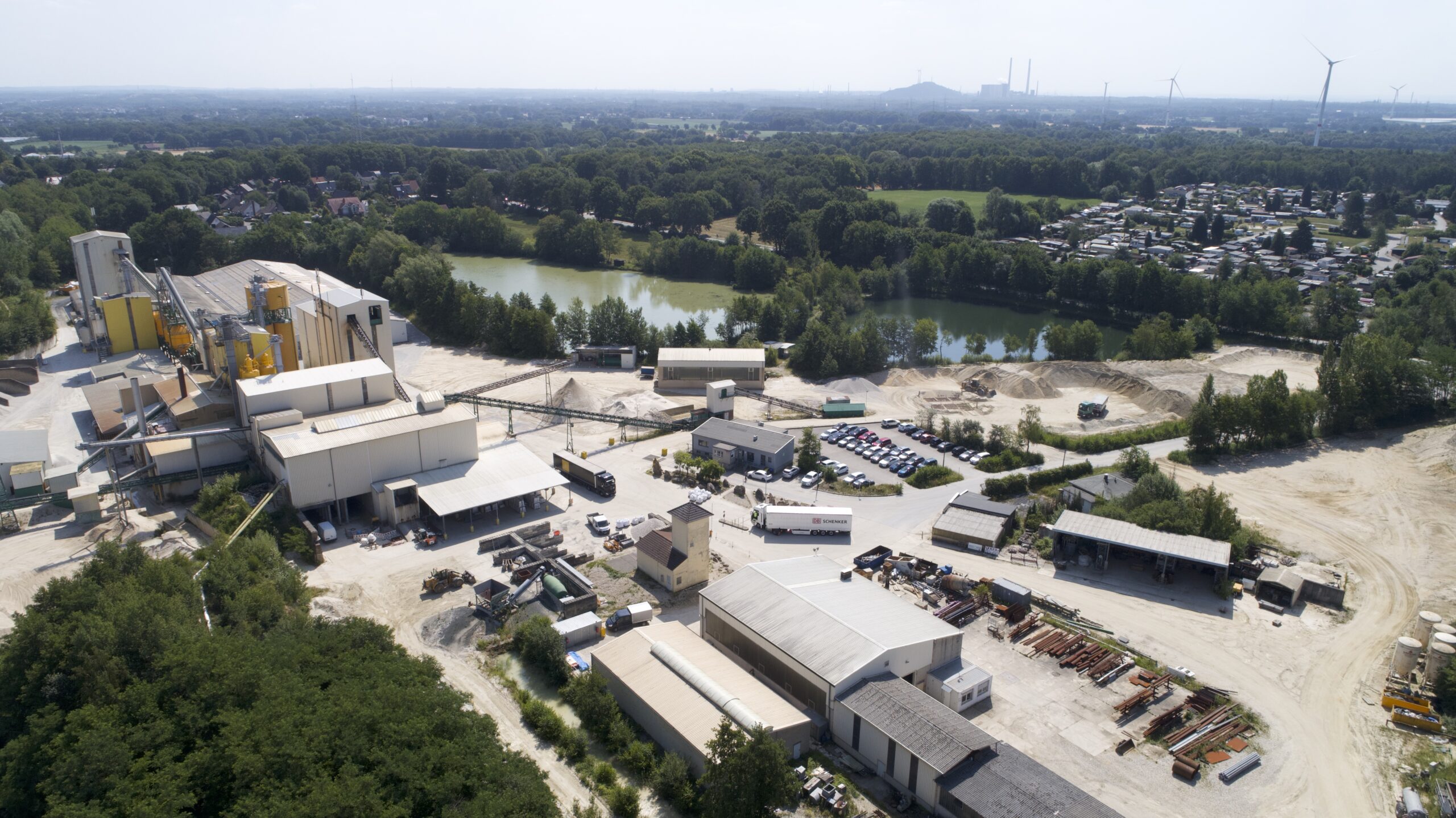
Thanks to Elara, we now have seamless access to machine history and maintenance reports. Being able to view object information and nameplates directly on site saves us valuable time. – Andreas Nienhaus, Maintenance Manager
The company specializes in the extraction and processing of quartz sand and quartz gravel. It sells processed sands and gravels, either moist or dry, in various packages, as well as loose, to customers. The product range extends from simple construction sand to high-quality filter gravel for drinking water treatment, representing a broad product spectrum. In addition, the company refines the material into high-quality dry mortars and other products in its mixing plants as a contract manufacturer on behalf of customers.
An interview with Andreas Eckrath, Operations Assistant, and Andreas Nienhaus, Maintenance Manager, from EUROQUARZ GmbH
What specific challenges or problems did your maintenance have before using Elara?
Before using Elara, we faced some challenges in our maintenance. Tasks were often forgotten as we mainly worked with Post-it notes or verbal information. Maintenance reports were kept in Excel and on paper sheets, which led to additional work when there were changes in the process flow. There was a lack of complete machine history, which led to issues and plant stoppages. It wasn’t easy to track repairs and maintenance work.
How has Elara helped your maintenance to solve these challenges?
Elara offers a scheduling function and reminders to ensure no tasks are forgotten. Machine History is now correctly documented; employees can enter smaller tasks directly from their smartphones. Complete documentation of job details, creation, and completion times is of great importance to us. Elara has replaced the previous Excel lists. Now all supervisors can access their maintenance reports during audits. Circuit diagrams and documentation of the installations are accessible to all.
Read on now: How Elara supports businesses!
What specific features or aspects of Elara have helped your maintenance the most?
Creating templates for repair orders or inspections has saved us a lot of time and enabled us to work efficiently. The management of objects, including sub-objects, has proven extremely useful, especially in documenting electric motors with stored type plates. In the past, when a fault occurred, an employee had to go to the equipment and photograph the performance data, which was time-consuming. With Elara, we can now access the objects and the type plates directly on-site, which is essential for orders and repairs. Maintenance management, especially for safety checks on machine tools and vehicles, has also been improved by Elara.
How easy was it for your staff to get used to using Elara, and how have Elara integrated into your users’ daily work?
Of course, our training period varies depending on the staff’s experience using smartphones and apps. Overall, however, Elara has quickly and effectively integrated itself into the everyday work of our users. The acceptance of Elara is continuously increasing.
What benefits has your maintenance experienced through the use of Elara?
By using Elara, we have improved our maintenance and repair management and simplified documentation. Information can now be easily moved back and forth between different tasks, for example, by attaching drawings to repair orders. In the past, sharing information was more cumbersome because it had to be printed out and passed on manually. With Elara, we can now retrieve wiring diagrams and other documents via the smartphone, which makes access and communication much more accessible.
How would you rate Elara’s customer service and support?
Elara’s customer service has responded quickly to our requests, as with the introduction of QR codes. We are delighted with Elara’s customer service and support.
Would you recommend Elara to other companies, and if so, why?
Yes, we would recommend Elara to other companies, mainly because of the uncomplicated set-up and intuitive operation. The operational structure and order management are easy to use, and most of the functions are self-explanatory. We have already successfully recommended Elara to a subsidiary, which is now also using the software. Another advantage is that Elara is a cloud-based software; therefore, no local Windows software needs to be installed.
What would you say is the unique selling point of Elara compared to other solutions?
The unique selling point of Elara is its highly intuitive operation. Unlike other solutions, which are often complex and confusing, Elara is characterized by user-friendliness and a well-structured overview.
Conclusion
The introduction of Elara has significantly improved our maintenance processes by enabling a structured and efficient management of maintenance and repair orders and a complete machine history. The user-friendly and intuitive operation of the cloud-based software has promoted acceptance among employees and optimized communication and information exchange. With responsive customer service, Elara has met our expectations, and we would therefore recommend it to other companies.
[In the age of AI, you never know if you’re reading something copy and pasted directly from ChatGPT, or if an actual human sat down to write this with some cool facts from their boss or operations team. That’s why we created a short and simple introduction to how we create content at Elara.]