With reliability and efficiency becoming increasingly important, maintenance strategies are shifting from reactive to preventive maintenance. The transition to preventive maintenance is an essential step for companies to [...]
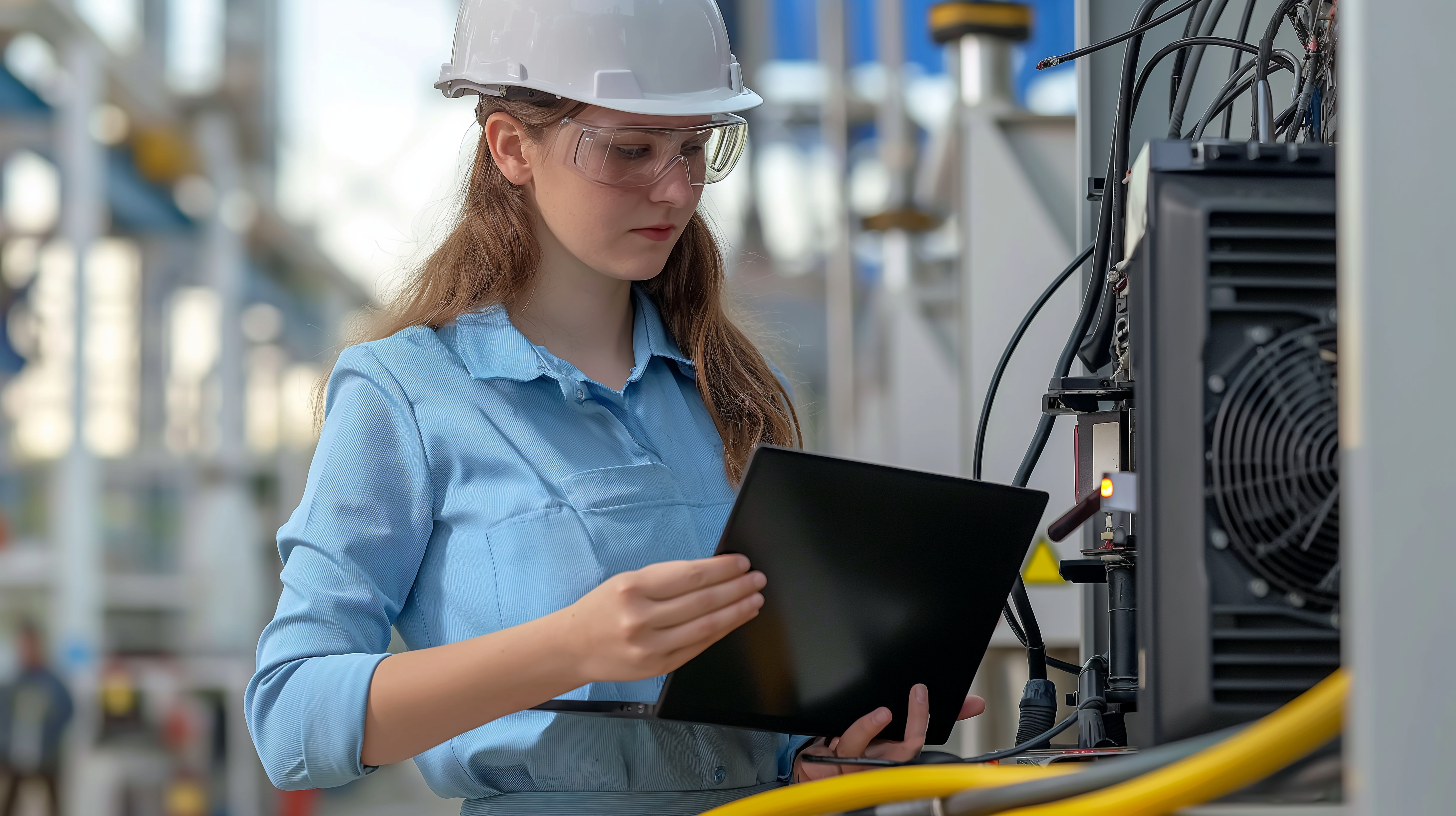
With reliability and efficiency becoming increasingly important, maintenance strategies are shifting from reactive to preventive maintenance. The transition to preventive maintenance is an essential step for companies to minimize downtime, reduce costs, and increase the overall efficiency of their equipment. Indeed, a McKinsey study also found that preventive maintenance is faster, cheaper, and less disruptive than reactive maintenance.
In this article, we’ll present six key steps that, in our experience, help companies successfully transition from reactive maintenance to preventive maintenance. We will illustrate each of these by using an example of a customer who successfully transitioned from a reactive to a preventive maintenance strategy with the help of Elara.
What is preventive maintenance, and what are its benefits?
Preventive, or proactive, maintenance aims to prevent machine and production system failures from occurring in the first place. To reduce or eliminate potential problems or failures of machinery, equipment, or systems, preventive maintenance activities are planned and performed in advance (before a breakdown can occur). The goal of preventive maintenance is to extend equipment life, improve operational reliability, and minimize unplanned downtime.
Companies and organizations benefit from preventive maintenance in several ways. First, there is the reduction of unplanned downtime. An Aberdeen study found that unplanned downtime is a silent productivity killer, costing industrial manufacturers an average of $260,000 per hour.
By performing regular inspections, maintenance and timely replacement of parts, potential problems can be identified early and corrected before they cause extensive downtime. This helps maintain productivity and reduce operating costs by eliminating the immediate costs and lost production associated with unplanned repairs.
Preventive maintenance also extends the life of equipment and machinery. Regular care and maintenance can reduce wear and tear, which in turn extends equipment life and reduces the need for expensive replacement investments. Longer equipment life not only pays for the initial investment but can also help increase the company’s profitability.
Furthermore, improved equipment reliability can increase customer satisfaction and enhance a company’s image by giving customers confidence in reliable products and services. Altogether, preventive maintenance offers a number of benefits that can improve both the efficiency and competitiveness of a company.
One of our customers, Zerzog GmbH & Co. KG, in the plastics industry, was struggling with a number of maintenance problems before using Elara’s maintenance software. Due to a lack of communication between production and maintenance teams, repair orders were not requested and completed on time, often resulting in longer downtimes. As a result, Zerzog’s maintenance team often had to respond reactively. Together we’ll walk through the 6 steps that we performed with the Zerzog team to move from a reactive to a preventive maintenance strategy. If you follow the same guidelines, this could help you move away from extremely stressful and costly “fire-fighting” operations and sustainably increase equipment efficiency and availability.
Step 1: Taking Stock
The first step was a thorough asset analysis. Zerzog’s team identified the assets and equipment that were critical to the smooth operation of the business. Next, they determined the maintenance intervals for these assets and how much downtime could be tolerated before it would seriously impact the company’s operations.
Step 2: Define maintenance intervals for preventive maintenance
Once the team had identified key assets, it was important to establish clear maintenance intervals. These intervals must always be carefully considered in order to have smooth operations and a minimum amount of downtime.
It is important to have an understanding of not only the manufacturer’s recommendations but also the specific requirements of the industry and the availability of maintenance resources. Understanding these factors will help ensure an efficient and cost-effective maintenance process.
Step 3: Create a maintenance plan
Zerzog’s maintenance team has created a detailed maintenance plan for each asset, which includes all required maintenance activities. When creating your own plan, it’s important that all maintenance activities are documented in a comprehensive and coordinated manner, taking into account the availability of technicians. The maintenance plan should be well structured with clear responsibilities for each team member. Periodically review the maintenance plan to ensure it meets current requirements and operating conditions.
As Zerzog began to use Elara for their maintenance needs, they made it easier to follow by making it accessible to their team members on their smartphones. This allowed them to create and record maintenance tasks on a regular basis, as well as attach images and videos to help speed up the troubleshooting process.
Step 4: Train maintenance team members
Zerzog provided maintenance team members with the training they needed to perform maintenance properly using the new Elara system. That included the necessary know-how to maintain and repair the equipment while using instructions on the Elara app to guarantee uninterrupted uptime.
When training your own team members, make sure to include both theoretical and practical elements to ensure that the maintenance team has the knowledge and skills to carry out effective maintenance.
Step 5: Using software applications for preventive maintenance
Zerzog was able to streamline maintenance processes and identify and resolve potential problems early, before unwanted downtime occurred, by using Elara’s maintenance software. Implementing Elara’s maintenance software enabled a preventive maintenance strategy, optimizing uptime and reducing costs. Preventive maintenance also helps reduce problem response time and increases team member safety.
Step 6: Continuous feedback and improvement
The Zerzog team carefully analyzed equipment performance and adjusted maintenance schedules and intervals accordingly to improve their maintenance operations. By continuing to optimize, Zerzog has been able to increase the efficiency of maintenance programs and continually improve equipment reliability.
Just as a result of the use of Elara’s maintenance software, Zerzog has been able to reduce downtime by 20 percent, as repair orders are now reliably ordered and completed.
To identify potential weaknesses in the maintenance plan and make targeted improvements, we also recommend regularly gathering feedback from team members and customers. To further increase efficiency and minimize downtime, a thorough analysis of performance data can also reveal trends that indicate where adjustments need to be made to the maintenance plan. This cyclical process of continuous improvement is critical to ensuring the optimal performance and reliability of your maintainable assets over the long term.
The importance of preventive maintenance
We believe that preventive maintenance is a fundamental pillar of ensuring the efficiency and reliability of day-to-day operations. Our belief is based on the recognition that the proactive identification and correction of potential problems with machinery and equipment is the foundation for smooth operations. Through the integration of preventive maintenance methods into work processes, downtime can be minimized and productivity can be continuously increased.
Organizations can face a number of challenges when transitioning to preventive maintenance, including the initial costs of implementing new technologies or training programs and the need to adapt existing operating procedures. Setting clear goals and priorities, allocating resources appropriately, and working closely with all stakeholders to ensure a smooth transition are key to overcoming these challenges. The example of the Zerzog team above shows that it can be done.
We understand that preventive maintenance is a series of steps taken to prevent problems from occurring on a machine. And, starting with an initial plan and inspecting existing equipment is the first step in implementing preventive maintenance activities. The required parts and actions are then listed in a corrective action plan.
Identifying and correcting defects before they become major problems is another important aspect of preventive maintenance. There are a number of different types of defects that maintenance teams need to be aware of, such as defects in raw materials or design flaws. Precision maintenance is the best way to prevent defects. In the transition from reactive maintenance to preventive and later predictive maintenance, there are best practices that can help with the transition. If you’re working with multiple branches or locations, standardization of equipment is important to maximize efficiency.
Moving from reactive to preventive maintenance takes effort, but it pays off in the end. Our experience shows this time and time again. Through effective preventive maintenance, companies can reduce costs, improve uptime and increase efficiency. By following these steps, you can optimize your maintenance programs and make your equipment more reliable.
Discover the benefits of using Elara from Zerzog GmbH & Co KG’s operations manager.
[In the age of AI, you never know if you’re reading something copy and pasted directly from ChatGPT, or if an actual human sat down to write this with some cool facts from their boss or operations team. That’s why we created a short and simple introduction to how we create content at Elara.]