With the ease of use via smartphones, we can now create orders and record them more regularly. The ability to attach pictures and [...]
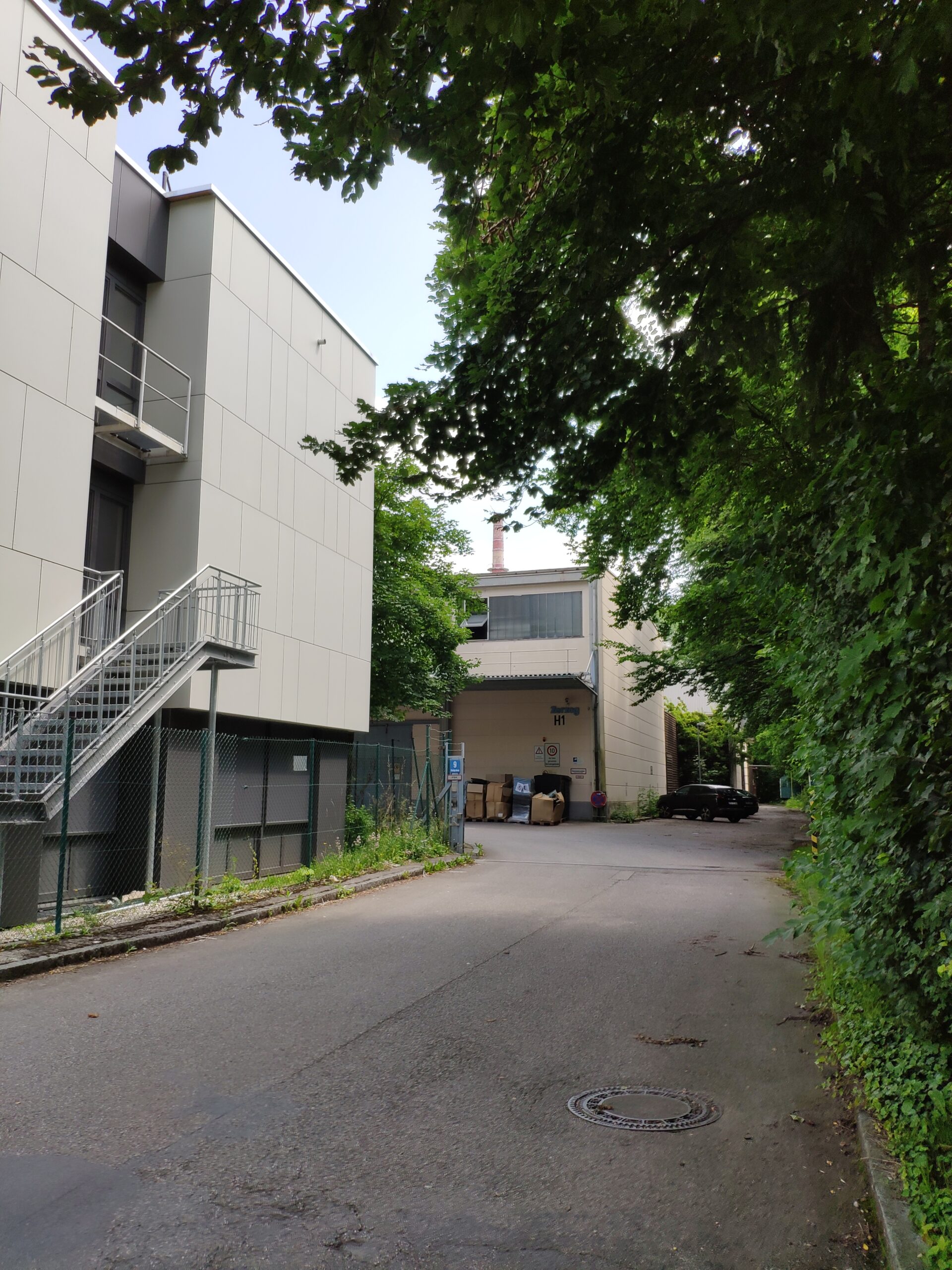
With the ease of use via smartphones, we can now create orders and record them more regularly. The ability to attach pictures and videos helps us troubleshoot. Previously, orders were recorded by email, which led to misunderstandings. With Elara, we have been able to reduce downtimes by 20%, as repair orders are now reliably commissioned and completed.
Andreas Grabmayer, Operations Manager, from Zerzog GmbH & Co. KG
The company Zerzog GmbH & Co. KG is a player in the plastics industry, specializing in the development and production of technical molded parts as well as packaging parts made of particle foams. It supplies various industries, including automotive, heating/sanitary, sports/leisure, food, transport, and the construction industry.
An interview with Andreas Grabmayer, Operations Manager, from Zerzog GmbH & Co. KG
What specific challenges or problems did your maintenance have before using Elara?
Before using Elara, we encountered some challenges in our maintenance. Insufficient communication between production and maintenance caused repair orders not to be placed or completed, leading to more extended downtimes. We neglected to document repairs, which led to repeated downtime due to similar defects. Another significant problem was the lack of adequate spare parts management, resulting in more extended downtimes due to lack of spare parts.
How has Elara helped your maintenance to solve these challenges?
Using Elara has helped us address these challenges. The ease of use via smartphones means we can now create orders and record them more regularly. The ability to attach pictures and videos helps us troubleshoot. We used to capture orders via email, which often led to misunderstandings. Now, with Elara, we reduce downtime by 20% by reliably placing and completing repair orders. We are also improving preventive maintenance through more consistent organization. Using Elara has also led to fewer discussions and disputes about breakdowns.
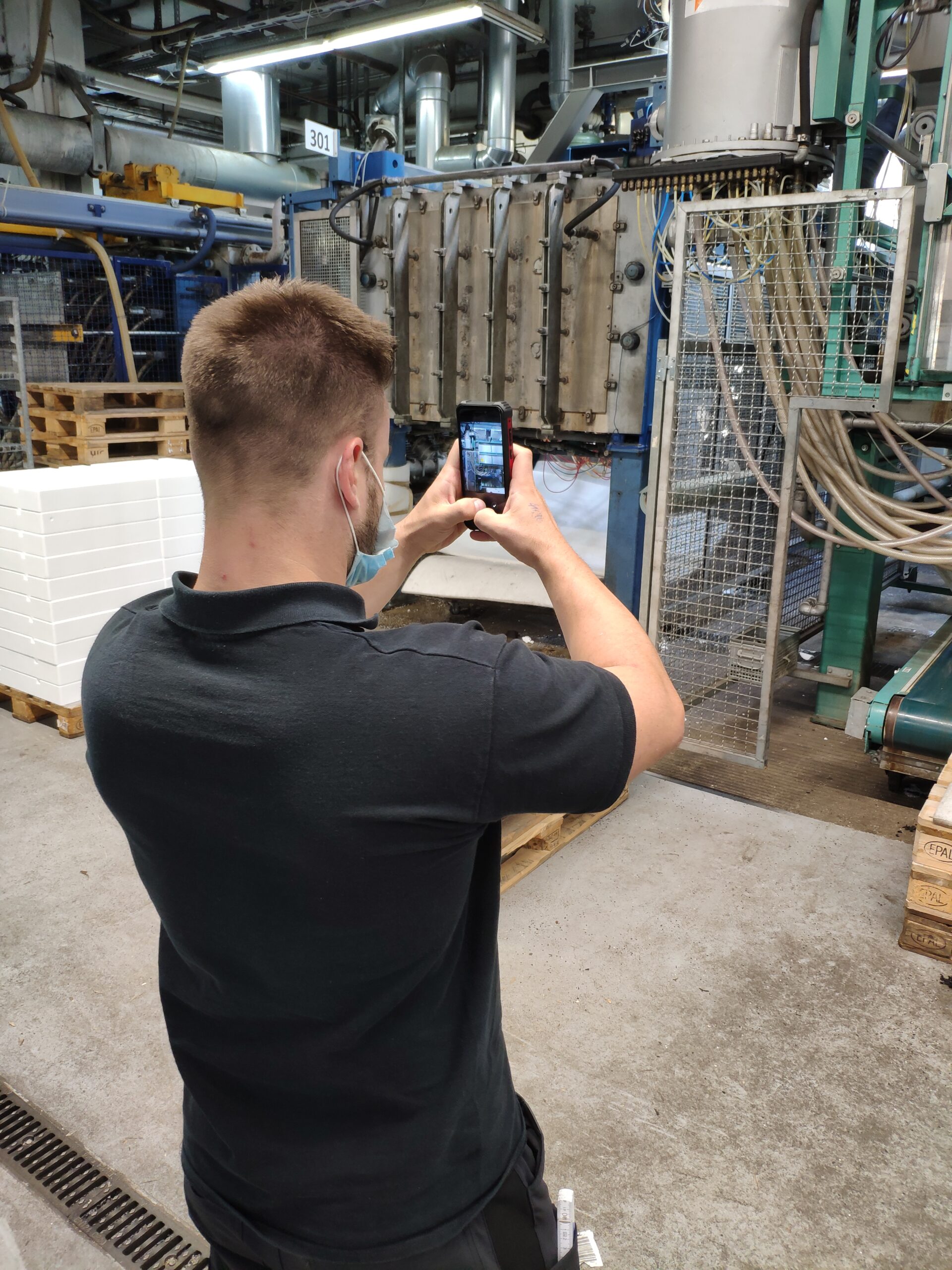
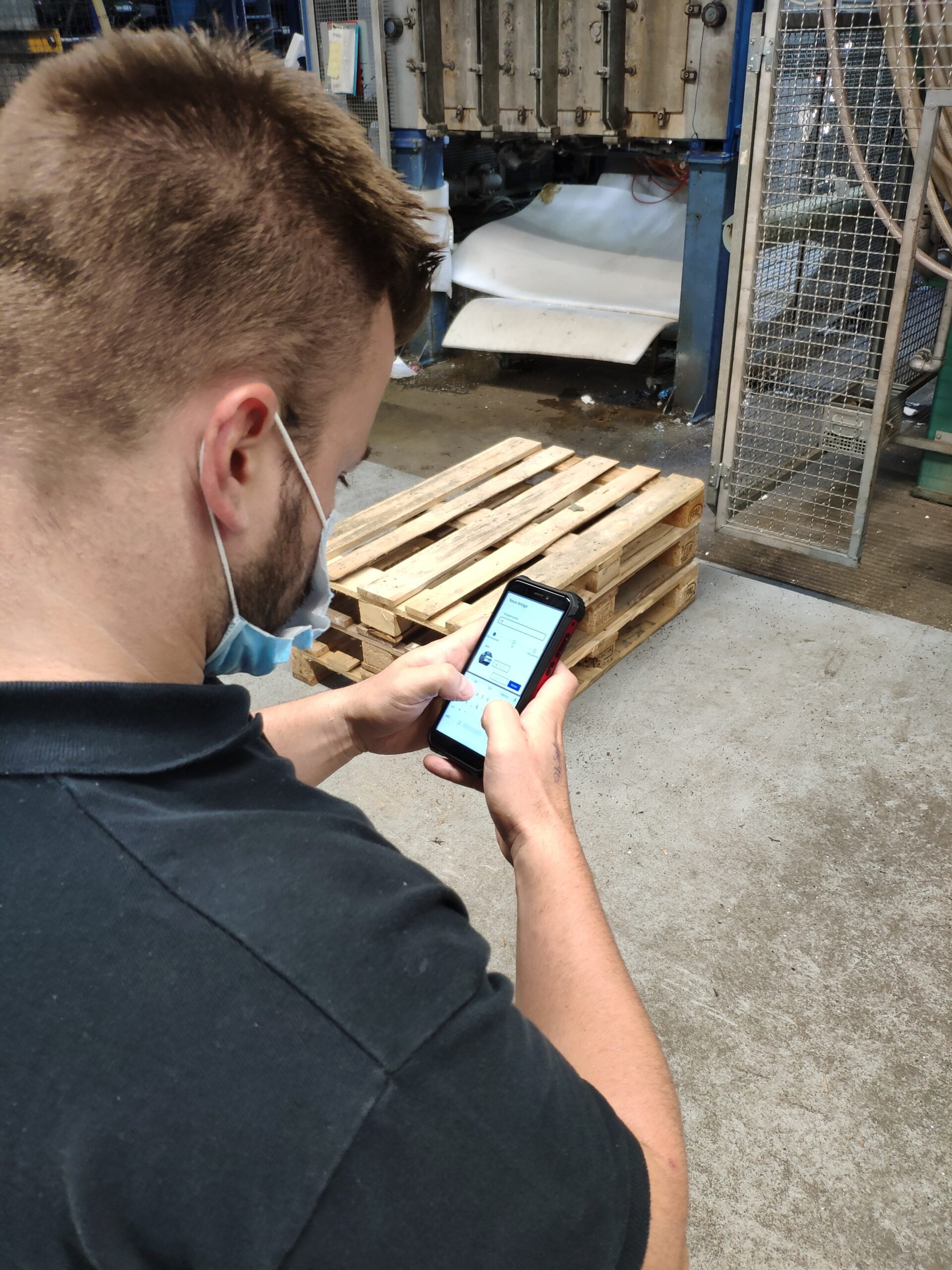
What specific features or aspects of Elara have helped your maintenance the most?
When entering an order, the photo and video function has proven extremely useful as it supports error analysis. The QR code function facilitates the quick creation of jobs.
How easy was it for your staff to get used to using Elara, and how has Elara integrated into your users’ daily work?
The staff found the introduction of Elara to be clear and understandable, which made the transition much more accessible. Although some production staff found handling the smartphone challenging, this did not affect the regular and reliable use of Elara in production and maintenance. Furthermore, the continuous improvement of Elara’s user-friendliness allows it to become even easier and more intuitive to use on an ongoing basis.
What benefits has your maintenance experienced through the use of Elara?
By using Elara, we have experienced the following advantages in our maintenance:
- We now prioritize and filter tasks according to different criteria. This gives us a more precise work plan and allows us to work more efficiently.
- The integration of photo and video material in Elara makes troubleshooting easier. Our employees capture and retrieve visual information on machines and tools directly in the application, which leads to faster diagnosis and repair.
- With Elara, we set and monitor maintenance intervals for tools. This prevents tools from not being serviced in time and causing breakdowns. We plan and carry out regular maintenance effectively.
Overall, Elara has helped to optimize our maintenance processes, increase efficiency and reduce downtime.
How would you rate Elara’s customer service and support?
Elara’s customer service and support are easy to reach and care for problems. In about 99% of cases, our concerns have been resolved satisfactorily so far.
Would you recommend Elara to other companies, and if so, why?
Yes, we would recommend Elara to other companies because the software is simple, user-friendly, and flexible. Elara offers a flexible solution for many challenges in production and maintenance. We already use Elara in our second plant in Traunreut.
Conclusion
Zerzog GmbH & Co. KG has significantly improved its maintenance processes with the help of Elara software. By applying a structured way of working, reducing troubleshooting, and carrying out effective preventive maintenance, we increase efficiency and reduce downtime. The Elara software has been able to integrate well into everyday work. Elara’s customer service impressed me with its accessibility and problem-solving ability. Given these positive experiences, Zerzog GmbH & Co. KG recommends Elara to other companies to optimize their maintenance processes.
Your time is precious, so that we will show you the advantages of Elara in a live demo. Book a product presentation now.
[In the age of AI, you never know if you’re reading something copy and pasted directly from ChatGPT, or if an actual human sat down to write this with some cool facts from their boss or operations team. That’s why we created a short and simple introduction to how we create content at Elara.]