A Computerized Maintenance Management System (CMMS) is software designed to help plan, monitor, and report on maintenance activities. It keeps track of all the relevant information, such as [...]
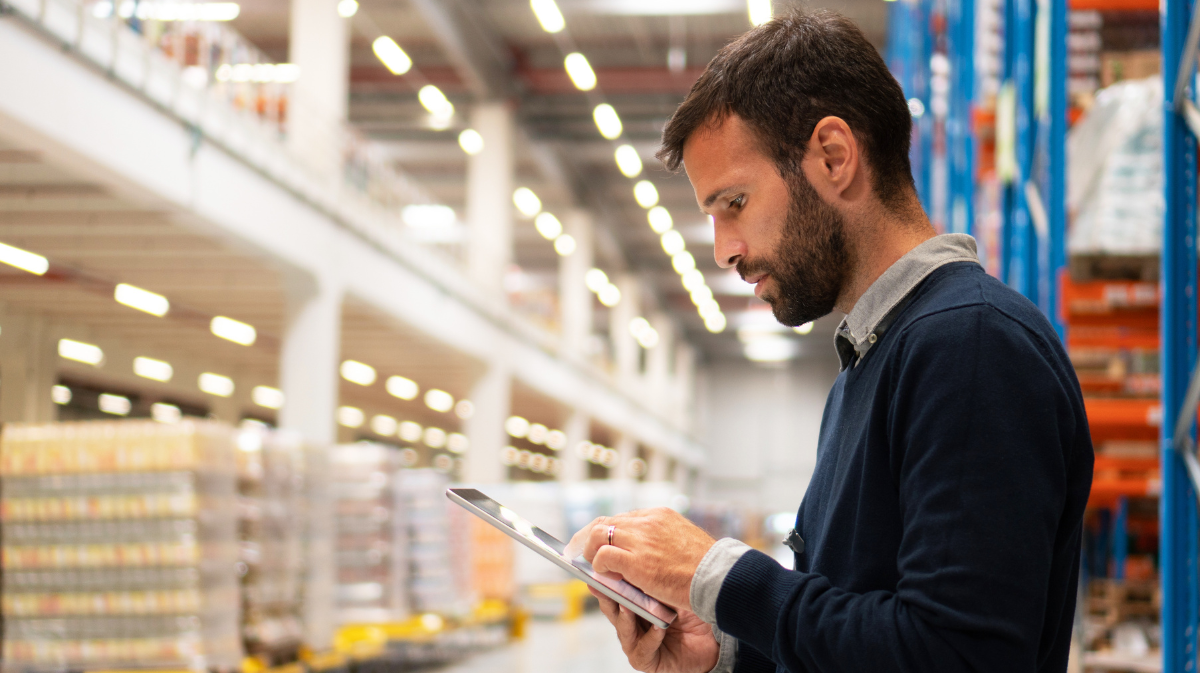
A Computerized Maintenance Management System (CMMS) is software designed to help plan, monitor, and report on maintenance activities. It keeps track of all the relevant information, such as the availability and usage of physical equipment and other assets.
Recently, IBM Maximo announced that it will discontinue support for its current version, 7.6, causing some upheaval in the CMMS landscape. Users are being encouraged to make the transition to the Maximo Application Suite (MAS) by September 30, 2025. MAS offers expanded functionality beyond traditional maintenance management software but can be significantly more expensive.
With change and rising costs, many maintenance teams are considering whether it makes more sense to switch to a new vendor or develop their own maintenance software. This process includes an evaluation of how each software simplifies work order management, eliminates duplication of effort, and focuses on increasing efficiency to save money.
Typically, when the number of machines, assets, or employees becomes too large to manage efficiently, companies begin looking for a CMMS solution. The amount of time and money lost due to inefficient processes is a good indicator that a company has reached this point.
What can I expect from using a CMMS?
With a CMMS solution in place, your teams will be able to execute work orders for machine repairs and inspections digitally. This may involve team members downloading an app to their phones or tablets. For those reviewing tasks on their computers, it’s often accessible through a web browser.
These tasks are called digital work orders. They allow team leads to create and assign tasks to different employees. Once a task is assigned, the person responsible receives a notification sent to their mobile phone or via emailed notification.
While this may seem simple on the surface, the scaling of a CMMS solution can be quite complex. Larger teams often operate in silos, using processes defined by specific teams or locations rather than those defined by the broader organization. Before implementing a CMMS, these processes need to be reviewed and adjusted to align with the organization’s goals, which may sometimes receive some initial criticism. This is normal. You are changing established processes that the team understands to new ones, which many have existed for years.
It’s a demanding process, but it’s a rewarding one because it gives everyone who needs to maintain machinery and equipment access to the data and processes they need without extensive training.
Let’s take an example to understand the impact of CMMS solutions a bit better:
Due to staffing issues, one of your maintenance teams at one plant is consistently over capacity, while another team at a nearby plant has an over-capacity of about one day. You can’t transfer a person from one plant to the other. That would create a four-day shortage at the first plant. Instead, you can use your CMMS to send one person from the overstaffed team to work one day a week at the other plant.
The tasks for that day are documented in the CMMS. The person can arrive at the plant and start working right away. Any questions about machines or where to find spare parts and tools can be answered using the app, ensuring immediate productivity. If that person goes on vacation, another member of the team can easily step in and fill in without a problem.
The team at the other plant appreciates the reliability of their colleagues. They welcome the extra help from someone who is already familiar with the tasks and equipment.
Benefits of using a CMMS for maintenance operations
Implementing a CMMS greatly improves the efficiency of maintenance operations. By digitizing work orders and centralizing information, teams can streamline workflows, reduce downtime, and increase overall productivity. The software ensures that all tasks are clearly assigned, tracked, and managed, eliminating confusion and duplication of effort. The result is faster response times, better resource allocation, and more effective maintenance planning, ultimately increasing operational efficiency.
Another major benefit of implementing a CMMS is cost savings. With better planning and preventive maintenance, companies can reduce the number of unexpected breakdowns and extend the life of their equipment. This proactive approach minimizes the need for costly emergency repairs and reduces the frequency of equipment replacement. In addition, CMMS helps optimize inventory management by ensuring that spare parts are available when needed. This prevents overstocking and reduces waste. All of these efficiencies translate into significant cost savings over time.
Improved regulatory compliance and safety are another two key benefits of using a CMMS. The software enables organizations to maintain accurate records of all maintenance activities. This ensures compliance with regulatory standards and internal policies. Automated reminders and checklists help ensure that inspections and maintenance tasks are performed on schedule. This reduces the risk of non-compliance. In addition, by keeping equipment in optimal condition, CMMS contributes to a safer work environment. This minimizes the likelihood of accidents and improves overall workplace safety.
The key features of a CMMS
Work order management is one of the core functions of a CMMS. Through a centralized platform, managers can prioritize tasks, monitor progress, and ensure that all necessary resources are available for each job. This ensures that maintenance activities run smoothly and effectively, reducing the likelihood of errors and delays. In addition, digital work orders help team members communicate and coordinate with each other, increasing overall productivity.
Another critical function of a CMMS is to help plan for preventive maintenance. The system helps prevent unexpected equipment failures and extends asset life by scheduling regular maintenance tasks. Based on usage patterns, manufacturer recommendations, or regulatory requirements, the CMMS can automatically generate maintenance schedules. This proactive approach reduces the risk of costly breakdowns and increases operational reliability by ensuring that equipment is maintained at optimal intervals. Automated reminders and alerts contribute to better equipment performance and longevity by ensuring that maintenance tasks are not overlooked.
Inventory and spare parts management is also a critical component of a CMMS. It helps maintenance teams ensure that the right parts are available when needed by tracking inventory levels in real-time. As a result, downtime due to waiting for parts to be ordered or delivered is minimized. To streamline the procurement process, the CMMS can also manage reorder points and automatically generate purchase orders. By maintaining optimal inventory levels, companies can reduce the costs associated with overstocking or stock-outs and ensure efficient and uninterrupted maintenance operations.
CMMS implementation: Challenges and solutions
One of the biggest challenges in implementing a CMMS is overcoming resistance to change. Employees may be reluctant to adopt new technology if they are accustomed to traditional maintenance practices. To move past this mentality, it’s important to get everyone involved from the beginning and to clearly communicate the benefits of CMMS and how it will support them in their role. At this point, it’s also helpful to use examples of problems the team faces on a daily basis, and how you got this tool to support them.
Afterwards, you’ll also need to provide them with thorough training. Identifying change champions within the team can also foster a positive attitude toward the transition and encourage widespread acceptance.
Another significant challenge is integrating a CMMS with existing systems. Organizations often have multiple legacy systems and processes that need to work seamlessly with the new CMMS. Ensuring that these are compatible and that data migrates smoothly can prove complex and time-consuming. Therefore, choosing a CMMS that offers robust integration capabilities and support is critical. By working with IT professionals and the CMMS vendor during the planning phase, potential integration issues can be identified and solutions developed before problems occur. A phased implementation approach can also minimize disruptions and ensure a smoother transition.
Want to learn more about how Elara can be used as a CMMS? Contact us to book a demo, and we’ll be happy to show you!
[In the age of AI, you never know if you’re reading something copy and pasted directly from ChatGPT, or if an actual human sat down to write this with some cool facts from their boss or operations team. That’s why we created a short and simple introduction to how we create content at Elara.]