Preventive maintenance involves carrying out routine maintenance tasks on a scheduled basis to prevent unexpected breakdowns in the future. In simple terms, it's about addressing issues before they [...]
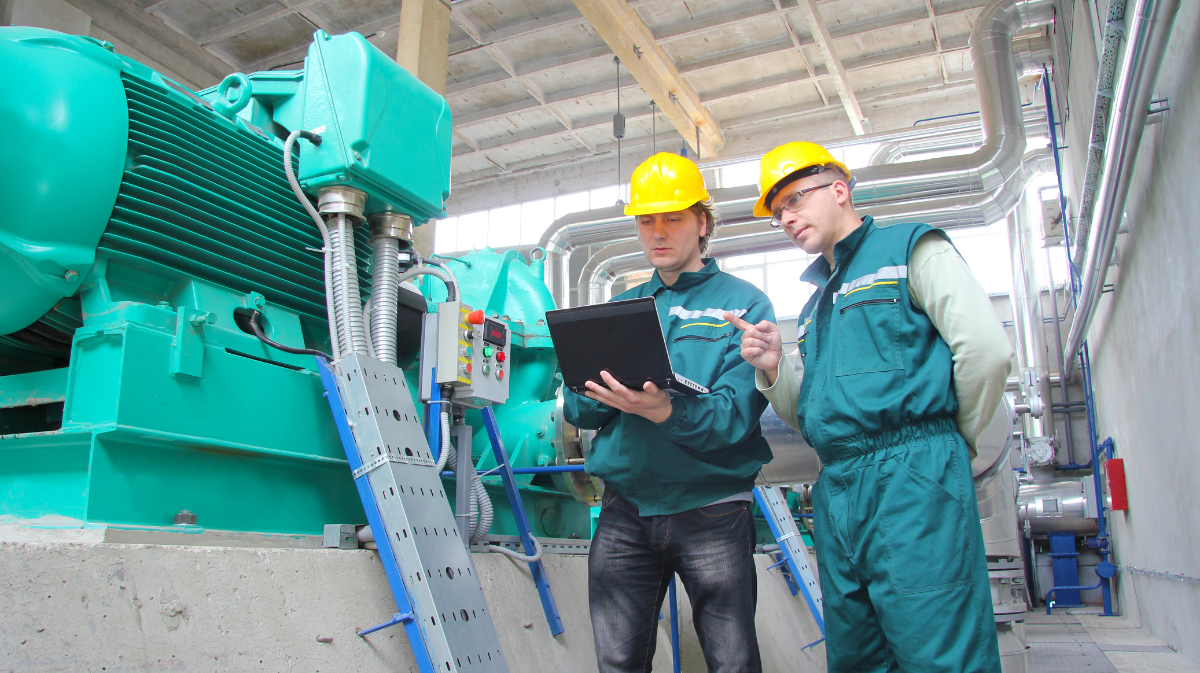
Preventive maintenance involves carrying out routine maintenance tasks on a scheduled basis to prevent unexpected breakdowns in the future. In simple terms, it’s about addressing issues before they lead to failure. You can read more about the specific benefits of the individual maintenance strategies on our blog.
Preventive maintenance is an essential part of effective maintenance management and is becoming increasingly important in industries such as production and logistics. Instead of only taking action when a machine breaks down, preventive maintenance focuses on proactively preventing breakdowns before they even occur. This not only ensures higher plant availability, but also reduces the overall costs of maintenance measures.
In this article, you will find out why many companies are changing their strategy from reactive to preventive maintenance and what the benefits are. We will show you how you can make your maintenance processes more efficient in order to minimize downtimes, extend the service life of your systems and reduce costs. You will also learn how a suitable software solution such as Elara can help you to successfully implement preventive maintenance in your company.
5 Benefits of preventive maintenance
Preventive maintenance offers numerous advantages for companies that prioritize reliable and optimized operational processes. We will now describe some of the key benefits in more detail:
1) Extended equipment lifespan
Regular maintenance is crucial for maximizing the lifespan of machinery and equipment. Preventive maintenance helps to detect and address signs of wear and tear early on, before they lead to major damage. Components that are regularly inspected and maintained operate longer and more reliably. This means that companies can delay costly replacements, reducing capital expenditure and increasing the long-term profitability of their equipment. Ultimately, regular maintenance ensures that machines perform optimally, extending the lifespan of the entire production infrastructure.
2) Minimizing downtime
Unplanned downtime is a nightmare for any company that relies on high production capacity. Not only do they cause considerable costs, they also lead to disruptions in operations that are difficult to rectify. Preventive maintenance aims to identify potential faults at an early stage and rectify them before they lead to machine failure.
Regular maintenance intervals allow problems to be identified and rectified at an early stage, reducing unplanned downtime to a minimum. This makes a significant contribution to increasing the productivity and availability of the systems. According to a study by Aberdeen Research, downtime costs companies an average of 260,000 US dollars per hour. This statistic highlights the importance of strategies to reduce machine downtime.
3) Cost efficiency
Preventive maintenance helps companies save costs in the long run. Emergency repairs are usually far more expensive than scheduled maintenance because they often lead to production downtime and may require last-minute procurement of spare parts and external services. In contrast, preventive maintenance allows for maintenance activities to be planned ahead, enabling more efficient use of resources. This makes it possible to order wear parts in advance and optimize replacement costs, resulting in a significant reduction in maintenance expenses.
4) Improved workplace safety
Another key advantage of preventive maintenance is improved workplace safety. Faulty or poorly maintained machinery poses a significant risk to employees and can lead to hazardous situations. Regular inspections and maintenance help minimize these risks by identifying and eliminating potential hazards early. Preventive maintenance ensures that machinery is always in a safe condition, greatly reducing the likelihood of workplace accidents. This not only contributes to employee well-being but also reduces liability risks for the company and the costs associated with accidents.
Preventive maintenance is therefore a long-term strategy that helps companies not only lower costs and increase efficiency but also improve workplace safety and extend the lifespan of their assets. A study by the European Agency for Safety and Health at Work found that reactive maintenance leads to more than twice as many accidents compared to preventive maintenance.
5) Improved product and service quality
Another significant advantage of preventive maintenance is the enhancement of product and service quality. Regularly maintained machines operate more consistently and reliably, leading to smoother processes and uniform production. When equipment is in optimal condition, the likelihood of production errors or deviations decreases. This enables companies to ensure that the products and services they provide meet quality standards, ultimately increasing customer satisfaction. Higher product and service quality also reduces return rates and rework costs, which strengthens the company’s competitiveness. Investing in preventive maintenance not only yields cost savings but also enhances brand image and customer trust.
Examples of preventive maintenance
Preventive maintenance encompasses a variety of measures aimed at enhancing the reliability of machinery and equipment. A common example is the regular inspection and maintenance of production machines, where wear parts such as bearings and seals are replaced before they can fail. Lubricating moving parts at scheduled intervals is also part of preventive maintenance to minimize friction and wear. In building maintenance, regular inspections of heating, ventilation, and air conditioning (HVAC) systems can help ensure operational functionality and avoid costly breakdowns.
Additionally, many companies leverage digital technologies like maintenance software to continuously collect data and respond proactively to performance deviations. These measures not only allow for targeted maintenance, but also optimize operational processes, ultimately leading to increased efficiency and cost savings.
Implementing preventive maintenance
The process begins with an inventory of the systems and continues with the creation of customized maintenance plans through to the use of a suitable software solution that enables efficient planning and monitoring of all measures.
Step 1: Inventory of equipment
The first step in implementing a preventive maintenance strategy is conducting an inventory of equipment. Companies need to gain a detailed overview of the machinery and assets in operation, identifying which ones are particularly prone to disruptions. Not all equipment requires the same frequency or intensity of maintenance; therefore, it is essential to identify the suitable candidates for preventive maintenance. Critical machines whose failure would have severe consequences for production should be a primary focus, along with those that have previously caused frequent issues.
Step 2: Developing effective maintenance plans
The next step involves developing effective maintenance plans. Companies should establish individual maintenance intervals and procedures for each piece of equipment, based on usage frequency, manufacturer recommendations, and past experiences. A well-thought-out maintenance plan ensures that maintenance tasks are performed on time, guaranteeing optimal machine operation without causing unnecessary downtime. Additionally, the availability of skilled personnel and spare parts should be considered to seamlessly integrate maintenance activities into operational workflows.
Step 3: Using a software solution
To manage preventive maintenance efficiently, the use of digital solutions is crucial. Modern software solutions, such as Elara’s Computerized Maintenance Management System (CMMS), assist companies in managing and monitoring their maintenance plans. Such software allows for the centralized planning, documentation, and tracking of maintenance tasks, ensuring better traceability and timely execution of activities. Digital solutions also enable the analysis of maintenance histories, providing valuable insights for further optimizing the maintenance strategy.
Common challenges in implementation from Elara’s perspective
Implementing a preventive maintenance strategy often comes with various challenges. One of the biggest obstacles we encounter with our clients is the skills shortage. Many companies struggle with a shortage of skilled personnel, limiting the availability of qualified maintenance staff. Additionally, financial resources for regular maintenance activities and training can pose a challenge.
Another barrier for many companies is overcoming organizational hurdles. Resistance may arise when introducing new maintenance strategies. Employees might be accustomed to existing processes and could question the need for change. It’s essential to address these concerns early and involve all stakeholders in the change process.
Furthermore, the successful implementation of preventive maintenance requires a cultural shift within the organization. This means fostering a long-term mindset that goes beyond short-term solutions. We consistently find that it is crucial for all employees to understand the benefits of preventive maintenance and work toward a common goal of enhancing the reliability and efficiency of the equipment.
How CMMS software supports preventive maintenance
The implementation of a Computerized Maintenance Management System (CMMS) is crucial for the successful execution of preventive maintenance. CMMS software like Elara allows companies to centralize their maintenance data and maintain an overview of all maintenance activities.
The advantages of using CMMS software are numerous. It provides efficient planning and monitoring of maintenance actions, ensuring that maintenance tasks are scheduled and executed on time. By automating work orders and analyzing maintenance data, companies can identify potential issues early and address them proactively.
For instance, companies like EGE GmbH and B-Plast have optimized their maintenance processes with the support of Elara. By utilizing CMMS software, they not only reduced the number of unplanned downtimes, but also significantly enhanced the efficiency of their maintenance strategies. These case studies demonstrate how CMMS solutions contribute concretely to the optimization of preventive maintenance.
Learn more about the benefits of preventive maintenance and book a demo of the Elara software to see how we can help you optimize your maintenance processes.
[In the age of AI, you never know if you’re reading something copy and pasted directly from ChatGPT, or if an actual human sat down to write this with some cool facts from their boss or operations team. That’s why we created a short and simple introduction to how we create content at Elara.]