With the help of Elara's maintenance software, we have successfully mastered the challenges of maintenance: the efficiency of our processes has been increased, costs reduced and the reliability [...]
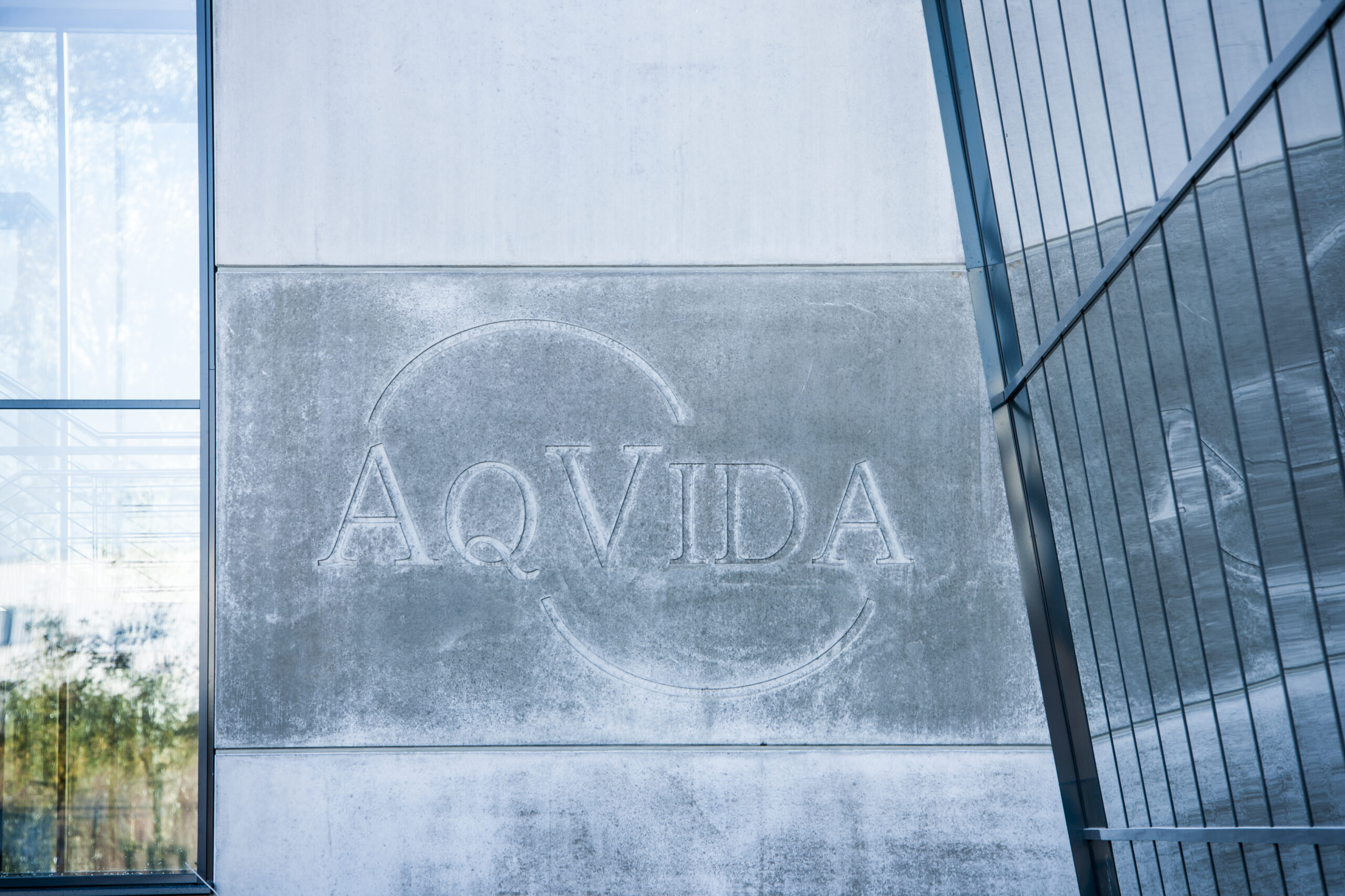
With the help of Elara’s maintenance software, we have successfully mastered the challenges of maintenance: the efficiency of our processes has been increased, costs reduced and the reliability of our plants significantly improved. – Thore Thöle, Team Leader Maintenance
The company, active in the pharmaceutical industry, has specialized in producing oncology products. The company is comparatively young by pharmaceutical standards but has already undergone a remarkable development from a pure distribution company to the establishment of an additional production site.
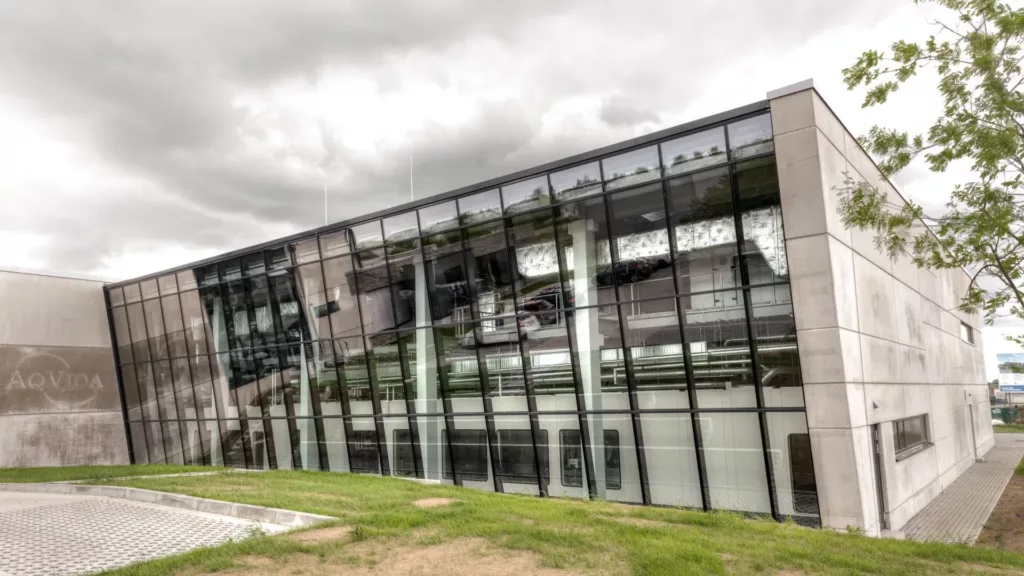
AqVida GmbH
An interview with Thore Thöle – Team Leader Maintenance of AqVida GmbH
What specific challenges or problems did your maintenance have before using Elara?
Before using Elara, our maintenance had to deal with several specific challenges and problems. Here are the individual points in detail:
- Spare parts inventory: Spare parts inventory was a problem because we did not have an efficient way to monitor the inventory and availability of spare parts. There was no central database or stock management system, which led to longer search times. This resulted in more extended downtimes as we were not sure if a needed spare part was even available.
- Asset logbooks: Before using Elara, we had normal logbooks where we could not give detailed descriptions. This led to a lack of transparency and made it challenging to check maintenance work afterward. It wasn’t easy to track the exact condition and history of the assets.
- Prioritization of tasks: Due to the lack of an overview of the different tasks and their prioritization, there were problems in processing them. In particular, tasks categorized as less relevant from F to G were neglected to receive the necessary attention. As a result, essential but not immediately urgent tasks were prioritized less, leading to potential bottlenecks in maintenance.
Overall, these challenges led to longer search times, longer downtimes, uncertainty in the availability of spare parts, and a lack of overview of the condition of the equipment. There was also a risk that essential calibrations were forgotten. There was no central point of contact for documentation, and there was no daily overview of maintenance tasks and processes.
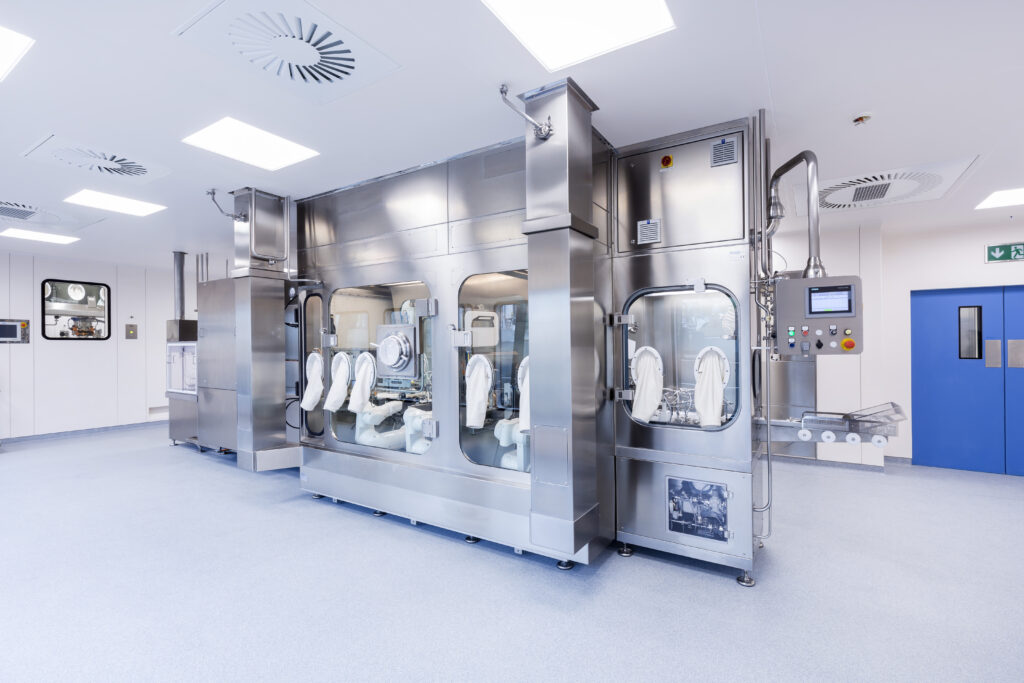
Plant of the company Steriline S.r.l from Como, Italy, Mirko Ebeling, at the company AqVida in Dassow, on 20.10.2016 in Dassow, Mecklenburg-Vorpommern, Germany, Europe
How has Elara helped your maintenance to solve these challenges?
Elara has helped our maintenance to overcome the above challenges through several features and solutions. Here are the specific improvements that Elara has brought:
- Improved traceability of condition changes at the facilities: Through Elara, we can now record detailed descriptions and information on condition changes at the facilities. Instead of the previous normal logbooks, we can now provide precise information on the maintenance work, repairs, or other changes that have been carried out. This gives us better traceability and transparency regarding the history and condition of the equipment.
- Efficient spare parts management: By using Elara, we can efficiently manage the stock of spare parts. The system provides better stock visibility, so we know exactly which parts we have in stock and where they are. This significantly shortens search times and reduces machine downtime, as we can now quickly access spare parts when needed. Furthermore, Elara also enables us to be alerted when a minimum stock level is reached.
- Evaluations of spare parts and material consumption: By evaluating the data, we can identify patterns and trends that help us to forecast material consumption better and take appropriate action. This helps to ensure that we always have sufficient stocks of critical materials and can avoid bottlenecks.
- Comprehensive task management and tracking: With Elara, we now have a central platform for managing and tracking maintenance tasks. We can record and organize all pending tasks, including maintenance, repairs, calibrations, and other tasks. This ensures that nothing is forgotten and all tasks are completed on time. Elara also allows us to assign tasks to specific team members and track their progress, which improves efficiency and collaboration in the maintenance team.
Through these Elara features and solutions, we have overcome the challenges. The use of Elara has led to more efficient maintenance by reducing search times, minimizing machine downtime, and improving the overall productivity of the maintenance processes.
What specific features or aspects of Elara have helped your maintenance the most?
Spare parts management was one of the functions that helped our maintenance the most. Elara reduced search times, gave a better overview of the spare parts inventory, and made it easier to place orders. Furthermore, Elara enabled comprehensive documentation of material consumption.
How easy was it for your staff to get used to using Elara, and how is Elara integrated into your staff’s daily work?
Using Elara was relatively easy for our staff, mainly because of the intuitive user interface. Elara has been well integrated into the daily work routine, and staff enters their tasks directly from meetings into the software. We use Elara for spare parts management, and in the future, we plan to put QR codes at the storage locations to record stock changes even faster.
How would you rate Elara’s customer service and support?
We rate Elara’s customer service and support as super and fast.
Conclusion
Elara has also helped us to have a better overview of the different tasks and their prioritization. With Elara, we can prioritize maintenance tasks efficiently and ensure that all tasks, regardless of their category, receive the necessary attention.
In summary, Elara has helped us to improve our maintenance processes. By having a better overview, more traceability, and transparency, we have gained a better insight into our maintenance activities. Mobile access to the software has enabled us to search for necessary documents and tasks at the point of action. This saves us time and costs and reduces machine downtime. We are delighted with the results we have achieved by using Elara and would recommend it without hesitation.
[In the age of AI, you never know if you’re reading something copy and pasted directly from ChatGPT, or if an actual human sat down to write this with some cool facts from their boss or operations team. That’s why we created a short and simple introduction to how we create content at Elara.]