The digitalization of maintenance processes is a crucial step for companies to increase their efficiency. Maintenance software can help optimize these processes and ensure better control over maintenance [...]
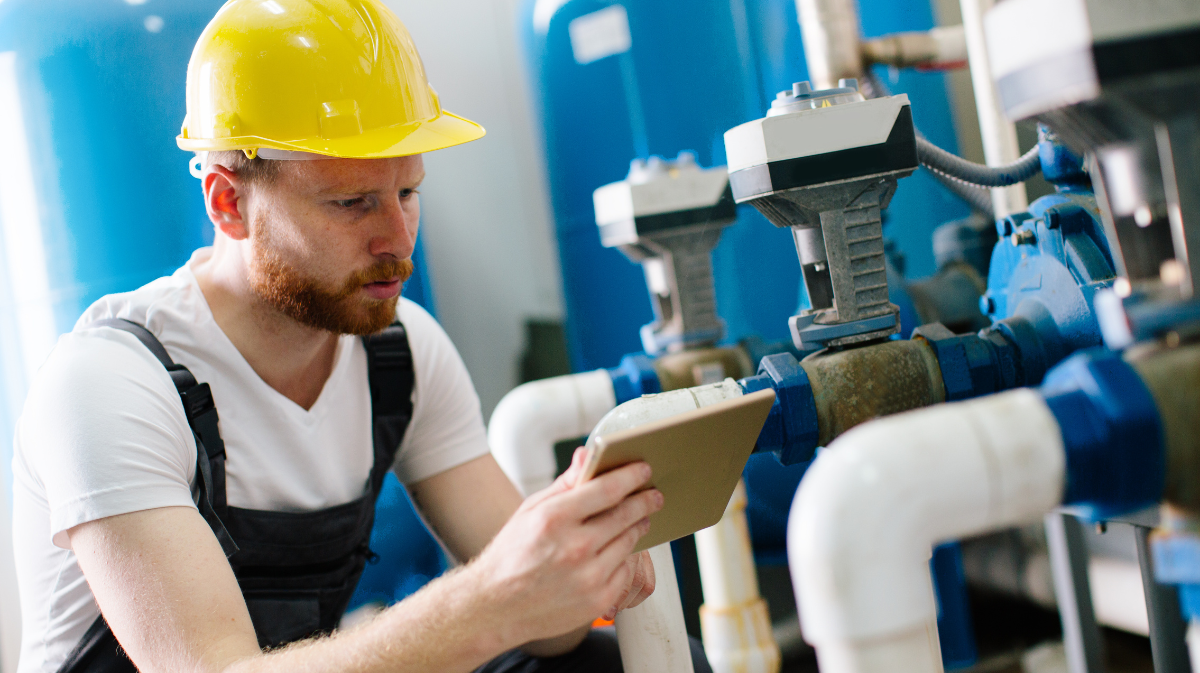
The digitalization of maintenance processes is a crucial step for companies to increase their efficiency. Maintenance software can help optimize these processes and ensure better control over maintenance tasks. We’ve summarized what maintenance processes truly entail in a recent blog article. In the following article we explain the benefits of implementing maintenance software and which factors we at Elara consider crucial for successful implementation.
Benefits of maintenance software
Maintenance software offers numerous benefits, some of which we have summarized in the following section. All these factors contribute significantly to optimizing the overall maintenance strategy and help companies increase their competitiveness.
Efficiency improvement
By digitalizing maintenance processes, tasks can be completed much faster and more accurately. This leads to a significant increase in operational efficiency, as maintenance tasks can be better planned and executed.
Automated notifications and scheduling functions ensure that no maintenance appointments are missed and help to minimize downtime
Cost reduction
Optimized maintenance processes significantly contribute to cost reduction. Through preventive maintenance and timely repairs, costly downtimes are reduced, and expensive emergency repairs are avoided.
Continuous monitoring of equipment allows for early detection of problems and targeted fixes before they escalate into more significant issues.
Transparency
Real-time data and comprehensive reports provide companies with a better overview of all maintenance activities. With maintenance software, all relevant information can be centrally recorded and analyzed.
This increases transparency and enables informed decision-making. Historical data on maintenance activities and equipment conditions can be easily retrieved, making it easier to plan future maintenance and optimize maintenance strategies. By implementing maintenance software, companies benefit not only from increased efficiency and reduced costs but also from improved transparency and control over their maintenance processes.
Challenges of implementing maintenance software
Implementing maintenance software presents several challenges for companies that need to be carefully addressed to ensure a smooth transition and fully leverage the benefits of new technologies.
1. Change in work processes
The implementation of maintenance software requires the maintenance team to adapt to new workflows and technologies. This can initially be challenging as established routines and habits need to be altered.
Onboarding is necessary to ensure that staff understands and can effectively use the new systems. Employee acceptance and engagement are crucial for the successful transition to new digital processes.
2. Integration of existing knowledge
Another important aspect of implementing maintenance software is the integration of existing knowledge. Current maintenance processes and the extensive expertise of employees must be incorporated into the software.
This ensures that all relevant information and best practices continue to be utilized and are not lost. Careful data migration and customization of the software to meet the specific needs and workflows of the company are essential in this process.
3. Clarity in responsibilities
To ensure a smooth workflow, roles and responsibilities must be clearly defined. Each team member should know exactly what tasks and duties they have and how these fit into the new digital processes.
This not only promotes efficiency but also accountability and employee engagement. A clear structure and communication are therefore crucial to avoid misunderstandings and ensure a seamless implementation of the maintenance software.
4. Lack of digital infrastructure
Companies without an existing digital infrastructure face technological challenges that require fundamental changes. Implementing maintenance software can be particularly complex if there is a lack of experience with digital processes.
There are numerous advantages to using cloud-based maintenance software. It is crucial that companies not only implement the software but also rethink and modernize their entire IT strategy to fully leverage the benefits of new technologies.
5. Human factors
The acceptance of new technologies may encounter resistance, as team members might be reluctant to embrace change. To overcome this hurdle, effective onboarding is essential to prepare the team for using the new software.
An open dialogue and continuous communication about the benefits and objectives of the software are also crucial to fostering engagement and acceptance within the team.
Elara’s tips for a successful implementation
Based on our expertise in the maintenance industry, we have identified the following factor that are crucial for the successful implementation of maintenance software:
Customized onboarding
An engaged onboarding team from Elara actively supports companies in setting up and implementing the software. They are available throughout the entire process to ensure a smooth implementation and effective training of employees.
We assist companies in analyzing and improving their existing maintenance processes. A detailed analysis helps identify and optimize inefficient workflows, thereby increasing overall efficiency and reducing operating costs.
User-friendliness of the software
Elara’s maintenance software stands out for its particularly user-friendly interface, which simplifies the introduction and use of the software.
An intuitive design enables employees to quickly familiarize themselves with the software and use its functionalities efficiently.
Mobile access
Elara offers a mobile application that allows users to access maintenance data and manage work orders on the go.
This feature supports flexible working methods and improves the maintenance team’s responsiveness to current demands.
Integration with existing systems
Elara’s software is compatible and can be seamlessly integrated with existing ERP and SAP systems and machine controls.
This integration enables automated data exchange and improved data consistency, leading to more efficient management of maintenance processes.
Customer support
Elara provides comprehensive customer support via email, phone, and chat to ensure that companies receive assistance whenever needed.
This includes help with technical questions, troubleshooting, and general support in using the software.
Conclusion
At Elara, we see the digitalization of maintenance processes as a crucial opportunity for companies to increase their efficiency and productivity. With user-friendly and comprehensively supported maintenance software, companies can not only optimize their maintenance processes but also achieve greater transparency and security.
Elara’s approach involves close collaboration with customers to develop customized solutions that meet the specific requirements and goals of each company. This ensures that the transition to digital maintenance processes is as smooth and effective as possible.
Want to know what our customers say about our Elara? Then check out our success stories.
[In the age of AI, you never know if you’re reading something copy and pasted directly from ChatGPT, or if an actual human sat down to write this with some cool facts from their boss or operations team. That’s why we created a short and simple introduction to how we create content at Elara.]