Efficient Maintenance Management through Elara Arne Bohlen, managing partner, and Birk Wagner, technical director of B-Plast 2000® Kunststoffverarbeitungs-GmbH, participated in an interview conducted by Akram Alraai, CEO of [...]
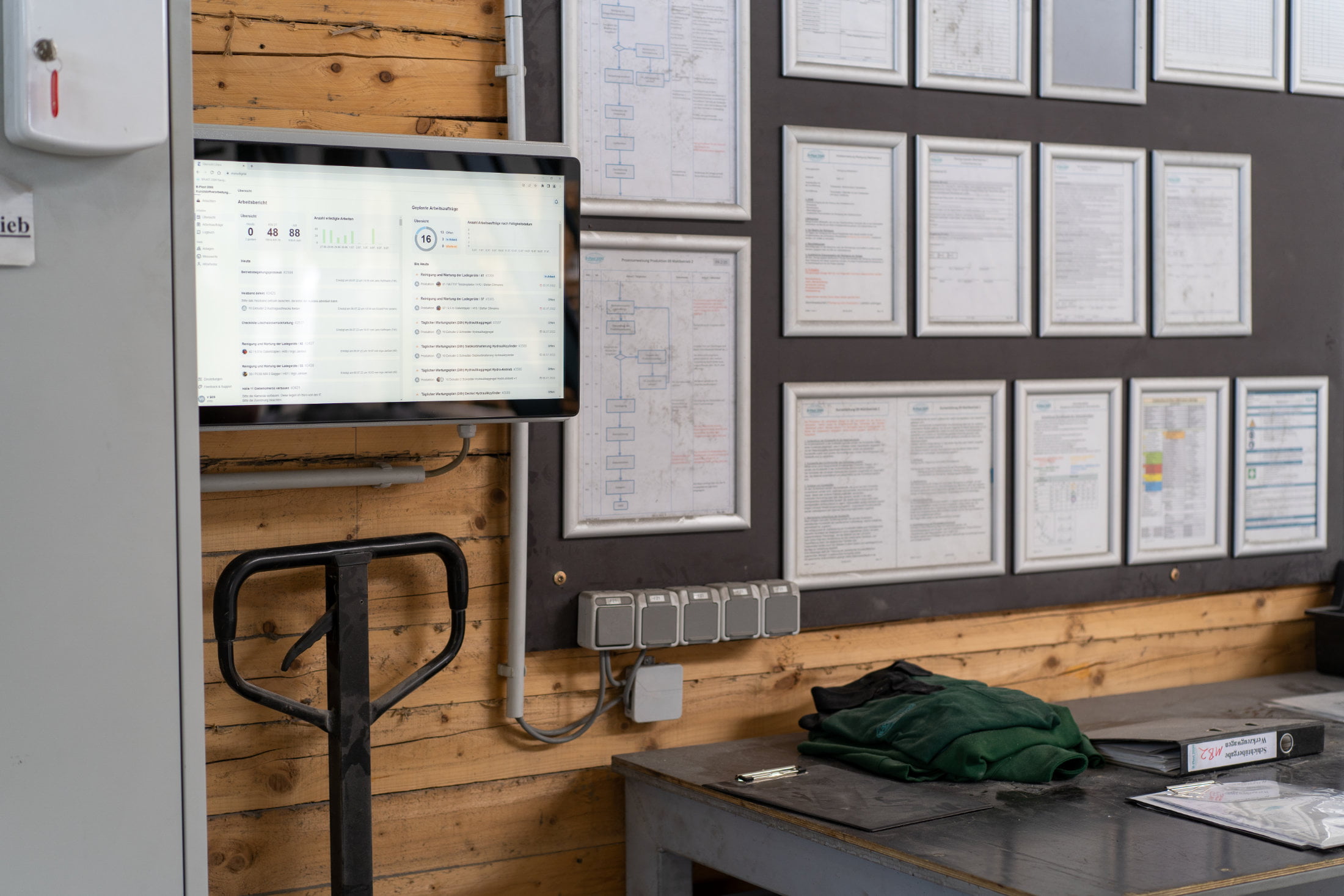
Efficient Maintenance Management through Elara
Arne Bohlen, managing partner, and Birk Wagner, technical director of B-Plast 2000® Kunststoffverarbeitungs-GmbH, participated in an interview conducted by Akram Alraai, CEO of Elara Digital GmbH. In the interview, they discuss how Elara has transformed its maintenance management.
Identifying and Solving Leaks
By involving employees and delegating responsibility, B-Plast 2000 identified leaks as the biggest issue in their facility using Elara’s logbook feature. These leaks led to high costs due to unplanned machine downtime. Thanks to Elara, they discovered the recurring leak issues and controlled them, reducing downtime.
Transparency and Innovation
Arne and Birk describe Elara as an innovative, transparent solution that offers a complete overview for all management levels and employees, down to the machine operator. They found Elara’s user interface visually appealing and easy to use. Employees are involved in planning, implementation, and controlling and can see what their colleagues are working on. Elara helps identify problems that were previously unnoticed.
Elara’s Impact on Collaboration and Problem-Solving
Elara has improved teamwork and communication within the company. Employees enjoy using Elara and can share information and problem descriptions more easily and track them at any time. With all information on work orders and projects stored in Elara, the duration of daily team meetings has been reduced from one hour to just ten minutes. When someone is absent due to illness, others can see this and take over tasks in Elara.
Improved Documentation and Access to Information
The most significant result of using Elara is accessing complete documentation via mobile devices. Problems can be identified and addressed more quickly, preventing them from escalating and incurring costs. Having all production events visible and accessible at any time has highlighted many pain points that were previously hidden. Important tasks that used to require time-consuming scheduling now appear automatically, freeing up employees’ minds and contributing to better workplace health management.
Elara: An Easy-to-Use Solution with Essential Features
When looking for software solutions, B-Plast 2000 valued features like the ability to attach documents such as photos or PDFs and Elara’s ease of use for all users. All employees now use mobile devices to access Elara, and the more people use it, the more it thrives.
Elara: A Browser-Based Solution for Greater Flexibility
B-Plast 2000 chose Elara because it is browser-based and can be used anywhere without needing an app or device-specific installation. This eliminates the need for IT involvement and offers device independence. They found other programs to be less user-friendly and more cumbersome.
How Elara Streamlines Daily Operations
A typical day at B-Plast 2000 starts with checking emails and Elara, reviewing weekend activities, and open tasks. In the facility, touch monitors display tasks for different areas, allowing colleagues to see what needs to be done. About 95% of the company’s operations are managed through Elara, which has replaced previous tools like OneNote.
Recommendations and Applications for Elara
B-Plast 2000’s management would recommend Elara for its mobile access, ease of use, and visually appealing interface. The platform allows users to capture ideas, assign tasks, and manage projects without anything falling through the cracks.
Elara is also used for various projects, from infrastructure investments such as production and storage facilities to machine planning. It is also employed in dispatch, order processing, and exports. Every department has a connection point with Elara, which has been integrated with the existing ERP system. This integration allows the warehouse to manage all incoming and outgoing goods with checklists and milestones displayed on monitors.
Before and After Elara: A Transformation in Maintenance Management
Before Elara, B-Plast 2000 relied heavily on Excel spreadsheets, paper records, and various digital tools such as Outlook email and calendar, OneNote, PDFs, and Microsoft Teams. Since adopting Elara, they have reduced their reliance on paper and analog processes, making their work faster and more effective. Communication and knowledge transfer have also been significantly improved.
Employees can see each other’s tasks in real-time, leading to a smoother workflow and more efficient task management. Before Elara, the technical director would have needed to carry more than 40 folders when moving offices; now, they only need the folder with invoices. Important documents like operating manuals, schematics, and other records are now stored in Elara, directly linked to the relevant objects.
The increased transparency has led to employees taking greater care with maintenance tasks, ensuring better equipment handling and more conscientious work. Overall, Elara has greatly improved B-Plast 2000’s maintenance management processes and contributed to a more efficient, collaborative work environment.
[In the age of AI, you never know if you’re reading something copy and pasted directly from ChatGPT, or if an actual human sat down to write this with some cool facts from their boss or operations team. That’s why we created a short and simple introduction to how we create content at Elara.]