The question of maintenance’s role in a manufacturer's sustainability plan is not an easy one to answer. It depends on the company, the products and services it offers, [...]
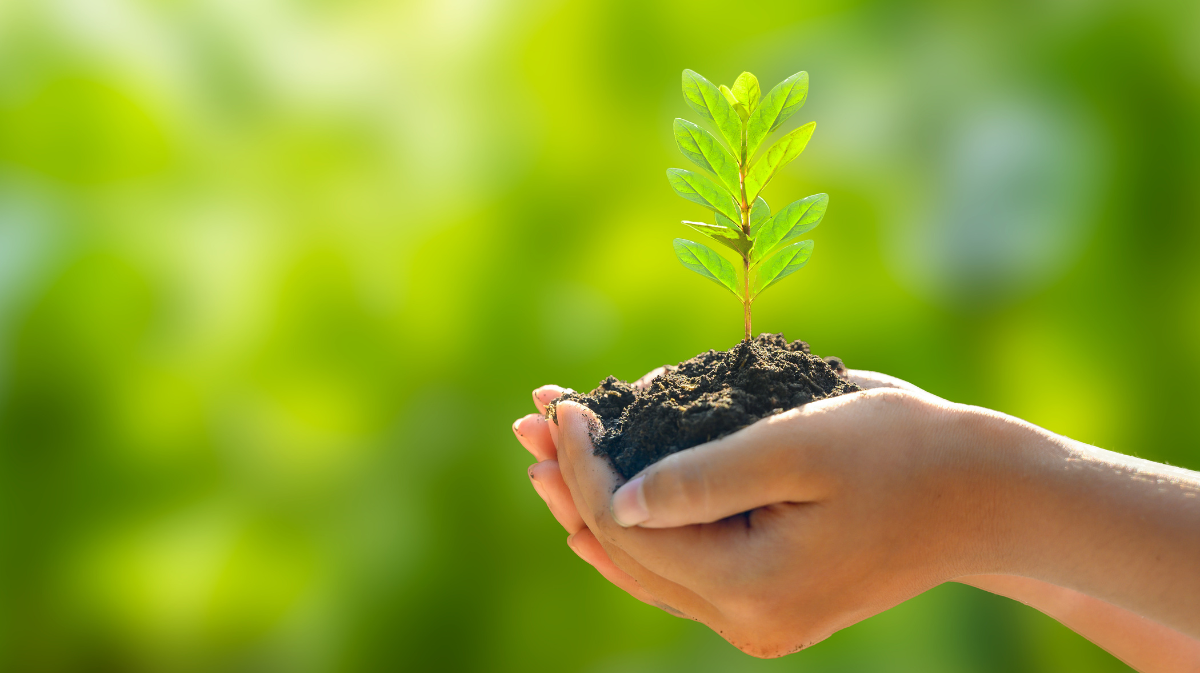
The question of maintenance’s role in a manufacturer’s sustainability plan is not an easy one to answer. It depends on the company, the products and services it offers, and its specific circumstances.
From material procurement and the production processes of small manufacturing companies to waste management in the industrial group, resource and energy consumption is moving higher and higher up the list of business priorities. All these examples have one thing in common: well-functioning machines and perfectly planned processes are the be-all and end-all. And this is precisely where sustainable use plays an important role.
Why is sustainable machine use so important?
In production, every mistake has costs: machine downtime, wasted working time, and wasted resources, to name a few possibilities. And it’s easy for this to happen, not because manufacturers are negligent, but because sustainable machine use requires routine care of individual components. These routine tasks may include regular inspections, lubrication, cleaning and maintenance, replacement of worn parts, and checking and calibration of measuring and control devices.
Despite their importance, these important tasks are easily forgotten, and the more carelessly manufacturing companies handle this issue, the more frequently unplanned downtimes occur. Consistently completing these tasks ensures the efficiency and reliability of machinery assets, leading to longer life, less downtime, and reduced maintenance costs.
Consider the humble bearing, an integral part to a huge number of machines. When given regular maintenance lubrication, bearings need to be replaced less often, and thus have a longer service life. This leads to a reduction in maintenance costs and higher plant availability.
Another example are rubber seals, which benefit greatly from sustainable use. Regular inspection and timely replacement of worn seals can prevent leaks and damage to machine components. This helps to extend the life of the machine, avoid costly repairs, and decreases the risk of hazardous externalities.
Sustainable machine use is conscious machine use, and correlates directly with longer service lives, reduced downtime, and increased savings. When sustainable manufacturing practices are integrated on a wider scale, whole plants can be made more efficient and resilient. It’s an incredibly scalable approach to use and maintenance that incurs low short term costs but high long term savings.
What are some examples of sustainable manufacturing tactics?
While there are many strategies for sustainable manufacturing machine use, an increasingly common method is through maintenance software such as Elara. These softwares offer a wide range of functionality, clustered around task management, machine asset databasing, predictive maintenance, monitoring/reporting, spare parts management, and knowledge capture.
With such a diverse toolbox, there’s a lot that manufacturers can do to operate more sustainably. Though many of these initiatives may require changes to workflows, the short-term adjustment period is worth the long-term benefits.
Engage in predictive/preventive maintenance
The longer assets run, the less they need to be replaced–perfect when it comes to conserving more materials and reducing waste. Asset longevity can be extended through sustainable maintenance, which includes both preventive and predictive maintenance.
These two concepts work hand-in-hand; preventive maintenance ensures you’re swapping out parts before they break or keeping your assets lubricated, while predictive maintenance helps you figure out exactly when you need to undertake these pre-emptive repairs.
As an added bonus, maintaining machine assets regularly reduces the risk of spills, lowers emissions, and helps prevent dangerous catastrophic failures.
Ensure your assets are comprehensively cared for
Regular, thorough maintenance may require more part usage or work hours in the short term, but it is overwhelmingly beneficial over time. In addition to the advantages listed above, well-running machines are far more efficient in regards to fuel and energy consumption.
Use knowledge capture to educate and train
By using digital knowledge capture and easily-accessible asset information, manufacturers can more adequately educate their employees on how to handle waste and other potentially harmful materials. The ability to quickly find asset-relevant information also contributes to lower malfunctions, in turn reducing waste and energy usage while improving the health and safety of workers.
Create effective checklists (and stick to them)
With the right software solution, you gain a comprehensive overview of all tasks, making it easier to plan recurring tasks. An interactive checklist with concrete work steps helps to optimize the maintenance process and avoid mistakes when handling the machine. An example of such a checklist could look like this:
- Inspect the machine and its components for wear or damage
- Check the lubrication points and top up the lubricant if necessary
- Clean the machine and work area to remove dust and dirt
- Check and replace worn parts, such as bearings or seals
- Check and calibrate measuring and control devices to ensure functionality
- Document the work carried out and set the next maintenance date
Because it’s a systematic tool that presents all relevant steps and tasks within the scope of machine maintenance and servicing, a checklist ensures that nothing is forgotten. This helps avoid errors and contributes significantly to sustainable manufacturing practices.
Tackling Sustainable Manufacturing Challenges
A solid maintenance software solution isn’t just useful for reducing waste and unplanned downtime. With its numerous product features, a software like Elara helps firms deal with other challenges as well, including:
- Shortage of skilled workers: It’s no secret that many industries and companies are feeling the squeeze from a systemic qualified worker shortage. With intelligent and easy-to-use knowledge capture, firms can capture the existing knowledge of their experts or long-term employees, and then make it accessible to others. This can help in retraining workers or quickly onboarding new hires to cover staffing needs.
- Adaptability to change: In a constantly changing production landscape, companies must remain flexible and adaptable. Maintenance software makes it possible to react quickly to changes in production processes or the machines themselves by providing all the necessary information for maintenance and adapting the maintenance process to changing conditions.
- Compliance with legal regulations and standards: Strict legal regulations and standards must be adhered to when maintaining machinery–and these standards are even tighter when maintaining machinery in a sustainable way. Maintenance software helps companies ensure compliance by centrally managing all relevant information and documents and making them available when needed.
In mitigating these issues, a reliable maintenance software helps save costs time and money while simultaneously increasing the quality of work and the level of safety. By being proactive and methodical, maintenance software enables companies to make their production processes more sustainable and efficient.
Are sustainable manufacturing strategies worth it?
The long-awaited digital future is here. Raw materials are becoming exponentially scarcer, and the world of work has changed drastically. Keeping up with the times has never been more important. The benefits of sustainable machinery asset use are easy to understand: increased efficiency, reduced costs, and longer machine life.
Shifting workflows to be more sustainable requires planning and effort, but much of this effort expenditure is a one-time investment. After sustainable strategies are developed and implemented, the effort required to continue sustainably manufacturing is relatively low, and in some cases, it’s much easier to work sustainably than to deal with the externalities of working unsustainably.
Our perspective
Sustainability initiatives in manufacturing aren’t on the horizon–they’re here. What used to be an abstract concept has become a reality, and many tried-and-true methodologies must be revisited if a relatively seamless operation is to be accomplished. The good news is that many strategies for sustainable manufacturing are surprisingly easy to implement (once the decision units have admitted that change is required). Beyond initial adjustments and the “startup costs” of preventive maintenance routines, the effort of working more sustainably is surprisingly low. At this point, there’s little excuse to stick to more traditional (read: wasteful and costly) ways of doing things. It’s cheaper and legitimately better for everyone to make sustainable changes to their operations.
Seize the opportunity to increase sustainability and efficiency
Software like Elara makes it possible to be more sustainable, reduce costs, and increase quality simultaneously. Over 100 companies are already benefiting from Elara, making an additional positive contribution to securing our future.
Don’t miss your chance to discover in which areas Elara can increase sustainability and efficiency in your company and avoid unnecessary costs. Book a 30-minute product demo with our Managing Director, Akram Alraai, now.
[In the age of AI, you never know if you’re reading something copy and pasted directly from ChatGPT, or if an actual human sat down to write this with some cool facts from their boss or operations team. That’s why we created a short and simple introduction to how we create content at Elara.]