“The unique selling point of Elara is the uncomplicated and fast implementation as well as the direct access via QR codes to the information pages of the equipment. [...]
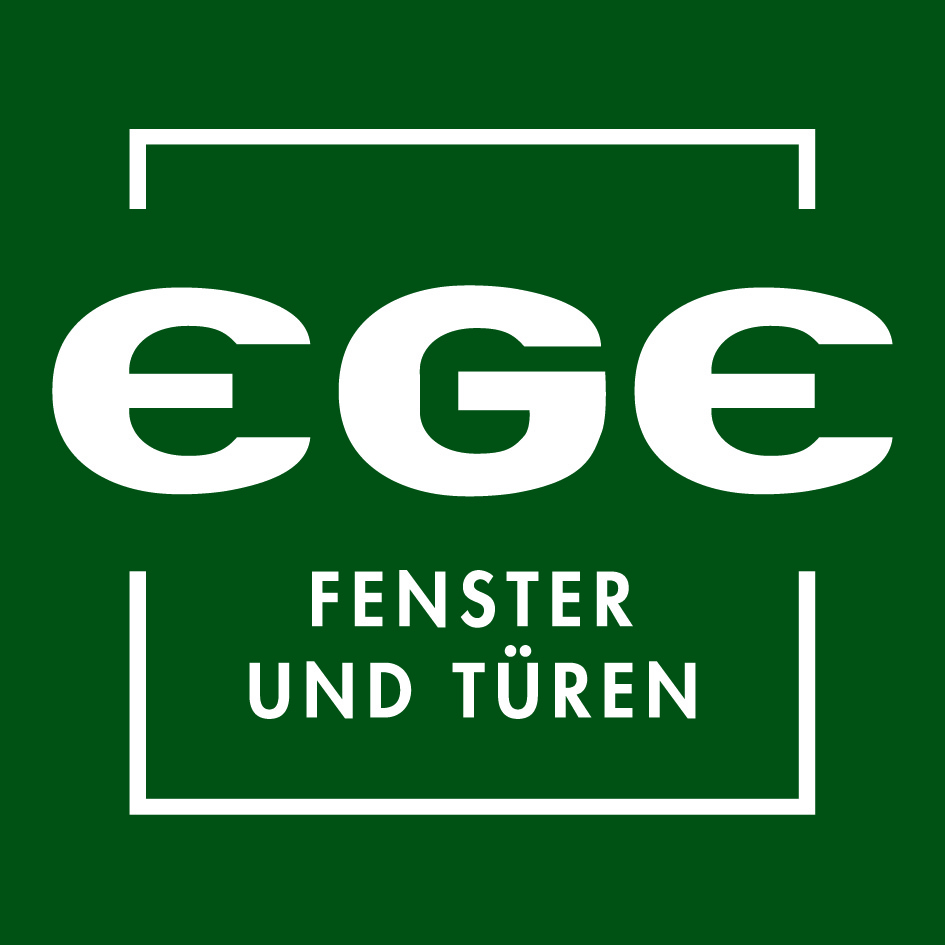
“The unique selling point of Elara is the uncomplicated and fast implementation as well as the direct access via QR codes to the information pages of the equipment. This function enables direct access to relevant data and documentation, which significantly increases the efficiency of maintenance processes.” Axel Schick – Operations Manager EGE GmbH
Since the 1970s, EGE has stood for commitment, progress and quality in the manufacture of high-quality windows and front doors. More than 400 employees and the will to always be a technical leader have spurred the company’s growth. Today, EGE produces at three locations in Germany using state-of-the-art technology and first-class materials.
Interview with Axel Schick, Operations Manager at EGE GmbH
1. What specific challenges or problems did your maintenance department face before using Elara?
Before the introduction of Elara, we faced several specific challenges in our maintenance:
- Decentralized inspection plans: Our inspection plans were not centrally available and were not consistently implemented. The workflow for managing compliance and documenting inspections was unclear and inefficient.
- Lack of collaboration: Maintenance tasks were not centrally coordinated or collaboratively managed with the involved process partners.This led to insufficient coordination and inefficient task management.
- Decentralized machine documentation: Important documentation and information about our machines was stored in different locations and was difficult to find. This made it difficult to access the necessary information and significantly delayed the maintenance processes.
2. How has Elara helped your maintenance team to solve these challenges?
Elara has significantly helped our maintenance team to solve the existing challenges as follows:
- Proactive inspection plan management: By integrating inspection plans with notifications, those responsible are now proactively alerted to upcoming inspections and their execution is monitored. The results of these inspections are documented centrally, whether for internal machine inspections or legally required inspections such as the testing of compressed air storage tanks.
- Efficient ticket system: Thanks to the new ticket system, team leaders and even employees (if created) can enter maintenance tasks directly at the machine. The ease of use of the system promotes acceptance and use, which leads to increased efficiency in task processing and the timely recording of necessary maintenance. As a result, both the mean time to repair (MTTR) and mean time between breakdowns (MTBR) are reduced, as minor defects are often rectified in good time before they lead to major problems and equipment failures.
3. What specific features or aspects of Elara have helped your maintenance the most?
Elara has significantly improved our maintenance through several functions. The integrated ticket system is particularly noteworthy, allowing our team leaders and employees to record and manage maintenance tasks directly on the machine. This direct recording not only improves the efficiency of work processes, but also helps to ensure that maintenance requests can be processed quickly, which in turn increases uptime.
Elara also helps us to plan and manage recurring inspection tasks. This function of Elara ensures that important inspections and checks are carried out regularly and reliably without being forgotten or neglected.
Another significant contribution is the machine-related entry points, particularly via QR codes. These enable quick access to relevant information and documentation directly at the respective machine. This not only facilitates maintenance and troubleshooting, but also access to crucial operating data, which in turn increases the overall efficiency of our maintenance processes.
4. How easy was it for your employees to get used to using Elara and how has Elara integrated into your users’ day-to-day work?
The introduction of Elara into the day-to-day work of our employees went smoothly and was quickly accepted. Elara’s user interface uses a consistent design, which makes it easier to apply functions once they have been understood to other areas. This enabled our employees to quickly find their way around and use the software effectively. It was particularly helpful that they quickly recognized a clear benefit from using Elara, which further promoted acceptance and integration into their daily workflow.
5. How would you rate Elara’s customer service and support?
Elara’s customer service is characterized by fast response times to inquiries regarding any errors or desired features. We were able to communicate easily both by phone and via Microsoft Teams, which efficiently supported the resolution of problems.
6. Would you recommend Elara to other companies and if so, why?
Yes, we would definitely recommend Elara to other companies. The platform offers a fast, cost-effective and efficient solution for implementing and carrying out preventive maintenance measures. Only a small amount of human resources are required to administer the solution, which is particularly attractive for smaller companies or those with limited resources.
7. What would you say is the unique selling point of Elara compared to other solutions?
Elara’s unique selling point is its quick and easy implementation, coupled with direct access to equipment information pages via QR codes. This function enables direct access to relevant data and documentation, which significantly increases the efficiency of maintenance processes. Elara also supports cross-platform use by a variety of end devices, ensuring flexibility and accessibility.
Want to find out more about Elara? Then book a free product presentation.
[In the age of AI, you never know if you’re reading something copy and pasted directly from ChatGPT, or if an actual human sat down to write this with some cool facts from their boss or operations team. That’s why we created a short and simple introduction to how we create content at Elara.]