Machine maintenance is the backbone of any efficient operational environment. Without a robust maintenance strategy, even minor malfunctions can cause unexpected downtime, severely affecting production and the bottom [...]
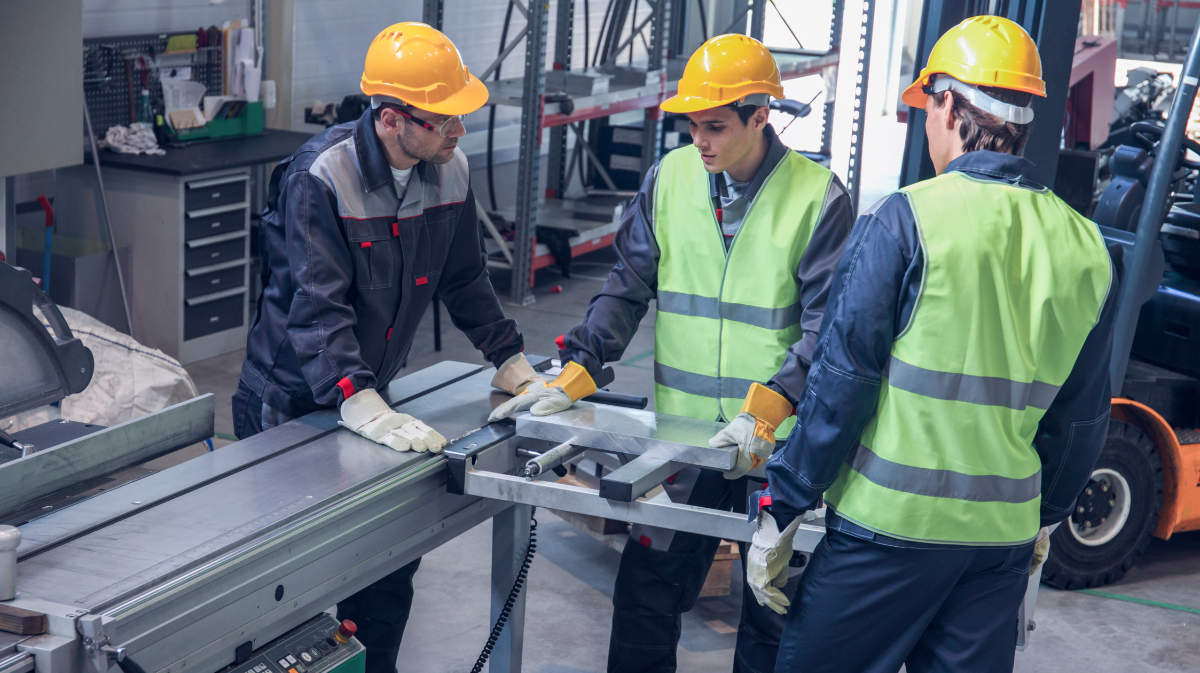
Machine maintenance is the backbone of any efficient operational environment. Without a robust maintenance strategy, even minor malfunctions can cause unexpected downtime, severely affecting production and the bottom line. In an era where digitalization is transforming every aspect of industry, optimizing machine maintenance presents a tremendous opportunity to boost efficiency and drive performance.
This is exactly where modern maintenance software comes in, helping companies to digitize manual processes, minimize downtime and make maintenance more efficient. In this article, we show how the digitalization of machine maintenance can transform operations and why maintenance software is essential for future-proof maintenance processes.
What is industrial machine maintenance?
Industrial machinery maintenance encompasses all strategies and processes necessary to keep equipment and systems in the best possible operating condition. This includes both preventive and corrective maintenance measures to ensure that the machines function efficiently, reliably, and safely.
Status quo of machine maintenance: challenges and problems
Despite technological advances in many areas of industry, machine maintenance is still carried out in the traditional, manual way in many companies. Maintenance work is often documented using pen and paper, which is time-consuming and prone to errors. This manual approach leads to a lack of transparency, as important information is not centrally available. It simply makes it difficult to track maintenance work and the condition of the machines.
The consequences of these outdated processes are far-reaching: production quality suffers as maintenance work is often overlooked or not carried out on time. This leads to unnecessary machine downtime and reduces the efficiency of resource utilization. In many cases, there is also incomplete or inefficient documentation, which makes it difficult to plan future maintenance measures and increases the error rate.
Typical challenges include:
- Overlooked maintenance tasks: Manual systems make it difficult to keep track of all upcoming tasks.
- Lack of transparency: The current status of the machines and maintenance work carried out are not easily visible to everyone involved.
- Inefficient use of resources: Employees and spare parts are not used optimally, which leads to longer downtimes and higher costs.
These problems illustrate that traditional methods in modern production are no longer sufficient to ensure efficient machine maintenance. This is where digitalization comes in to create transparency, automate processes and significantly increase efficiency.
Digital transformation of machine maintenance with the help of software
The digital transformation provides companies with a unique opportunity to elevate their machine maintenance practices. By implementing advanced maintenance software, organizations can not only automate manual processes but also enhance transparency, efficiency, and control. The advantages of digital maintenance are extensive, including the prevention of unnecessary downtime and improved resource utilization.
Real-time transparency and monitoring
A digital solution allows for real-time monitoring and documentation of all maintenance activities. Teams have constant access to crucial information regarding machine conditions, completed repairs, and scheduled maintenance. This increased transparency simplifies the planning and management of maintenance tasks, fostering a more organized and responsive approach to operations.
Optimized resource utilization
Effective machine maintenance leads to more efficient use of both personnel and materials. Intuitive maintenance software facilitates the creation of maintenance plans that maximize resource allocation and minimize downtime. For instance, timely ordering of spare parts and strategic deployment of staff help prevent machine outages, ensuring smoother operations.
Automation and proactive maintenance
One of the key benefits of digitalization is the ability to automate maintenance processes and implement proactive maintenance strategies. Rather than waiting for machine failures to occur, companies can continuously monitor machine conditions by collecting real-time data. This early detection of potential issues allows for timely maintenance interventions, preventing costly breakdowns.
Cost reduction and competitive edge
The synergy of enhanced productivity, decreased downtime, and improved planning can lead to substantial savings in maintenance costs. Companies that embrace digital solutions for machine maintenance gain a significant competitive advantage, enabling them to respond more swiftly and flexibly to changing production demands.
Overall, the digitalization of machine maintenance significantly optimizes the use of existing resources, enhancing production quality while simultaneously lowering operational costs. Modern software solutions provide all the essential tools for successfully implementing this transformation, allowing businesses to reap the long-term benefits of digital maintenance.
Elara: The solution for modern machine maintenance
Elara is a robust and comprehensive software solution tailored specifically to meet the needs of contemporary machine maintenance. With its extensive features, Elara empowers companies in the manufacturing, logistics, and airport industry to efficiently digitize and automate their maintenance processes.
Streamlined work order management
Elara allows for the centralized recording, management, and assignment of maintenance work orders to the appropriate personnel. The software offers real-time monitoring of work order progress, ensuring that all tasks are completed on time and to specification. This capability not only reduces the likelihood of errors but also helps to prevent delays in maintenance operations.
Comprehensive asset and machine management
Elara makes it possible to maintain detailed records of their machines and equipment, including technical specifications, maintenance requirements, and historical data. This level of transparency facilitates proactive maintenance planning, helping to minimize downtime and extend the lifespan of machines.
Efficient spare parts management
A key feature of Elara is its effective spare parts management system. Companies can monitor spare parts inventory in real-time and place orders promptly to prevent shortages. This capability plays a crucial role in ensuring that machines are quickly brought back into operation after maintenance tasks.
Meter and measured value monitoring
Elara’s meter and measured value monitoring functionality allows companies to capture and analyze essential measurement data, such as operating hours and temperature trends. This data provides valuable insights into machine conditions, enabling precise monitoring and facilitating preventive maintenance strategies.
AI Integration for enhanced maintenance
Elara takes machine maintenance to the next level by integrating artificial intelligence. With AI capabilities, companies can identify potential issues early and implement appropriate measures. Elara can answer critical questions such as “What was the last malfunction?” and “How did we resolve problem XYZ?” This feature enhances the efficiency of the maintenance process, driving improved outcomes.
Benefits of Elara for machine maintenance
Implementing Elara provides a multitude of advantages that extend well beyond mere process digitalization:
- Enhanced efficiency: By automating and streamlining maintenance processes, companies can significantly optimize their workflows. Work orders are handled more effectively, reducing downtime and allowing machines to be swiftly returned to operation.
- Minimized downtime: With preventive maintenance schedules and real-time monitoring, potential issues can be identified early, preventing breakdowns before they occur.
- Optimal resource utilization: Personnel and spare parts are allocated strategically, ensuring efficient resource use. This approach enables more effective planning and quicker response times.
- Improved product quality: A well-maintained machine infrastructure boosts productivity while decreasing error and scrap rates. This results in higher product quality and fewer customer complaints.
- Long-term cost savings: The synergy of reduced breakdowns, enhanced process efficiency, and improved maintenance planning leads to substantial cost reductions. Companies benefit from minimized short-term downtime expenses and long-term repair costs.
Case study: Proactive inspection plan management and efficient ticket system with Elara
Through the implementation of Elara’s maintenance software, EGE GmbH has significantly enhanced its inspection plan management and ticketing system. The integration of inspection plans with timely notifications ensures that the maintenance team is alerted well in advance of upcoming inspections and maintenance tasks, all of which are documented centrally.
Additionally, the ticketing system allows maintenance tasks to be recorded directly at the machine, greatly accelerating processing times. As a result, EGE has experienced a reduction in Mean Time to Repair (MTTR) and an increase in Mean Time Between Repairs (MTBR). This proactive approach enables minor issues to be addressed early, preventing them from escalating into major faults.
Read the full interview with EGE’s Operations Manager.
Why Elara is the best choice for machine maintenance
In an era where machine maintenance is becoming increasingly complex and demanding, Elara provides a customized solution for companies in the manufacturing, logistics, and airport industries seeking to modernize their maintenance processes. With features like digitalized work orders, real-time machine monitoring, efficient spare parts management, and AI integration, Elara is transforming how organizations manage their maintenance operations.
The advantages of Elara—such as enhanced profitability, reduced downtime, improved product quality, and long-term cost savings—make it a smart investment for companies aiming to elevate their machine maintenance practices. Elara is more than just software; it sets the new standard for future-proof and optimized maintenance strategies.
Curious about what our customers say about Elara? Check out our success stories to learn more!
[In the age of AI, you never know if you’re reading something copy and pasted directly from ChatGPT, or if an actual human sat down to write this with some cool facts from their boss or operations team. That’s why we created a short and simple introduction to how we create content at Elara.]