An effective inventory management system is essential for businesses in the production and logistics sectors. It ensures that inventory is accurately tracked, managed, and maintained at optimal levels [...]
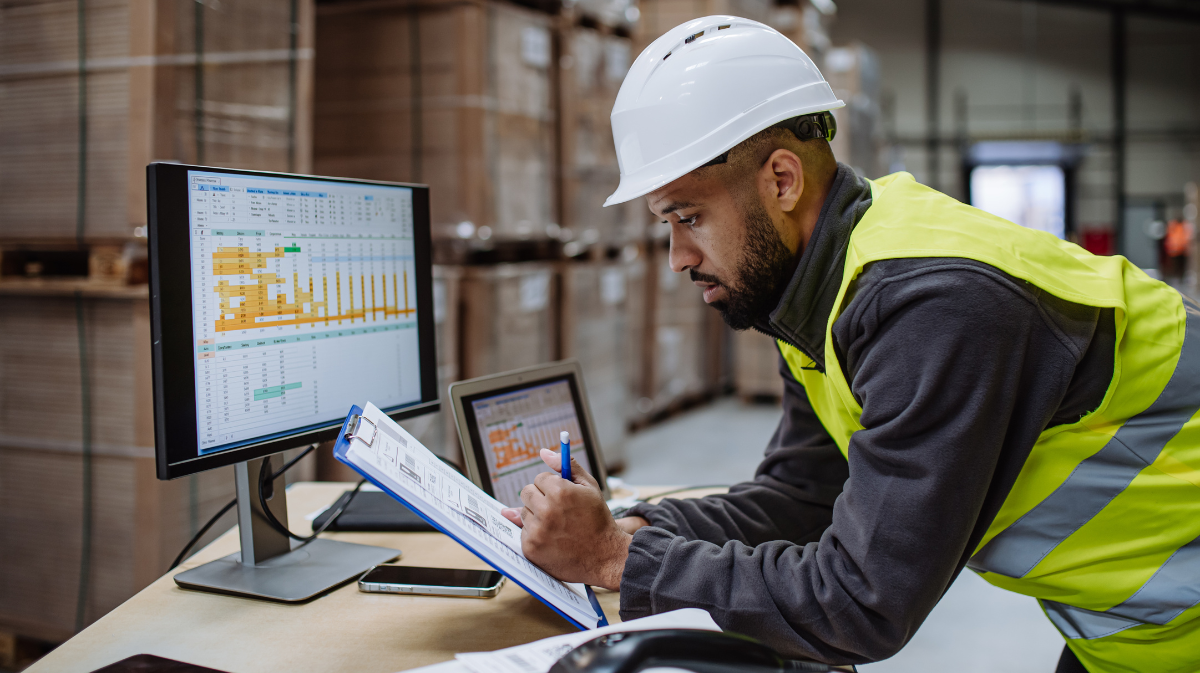
An effective inventory management system is essential for businesses in the production and logistics sectors. It ensures that inventory is accurately tracked, managed, and maintained at optimal levels at all times. Well-organized inventory control not only helps to avoid stock shortages and excess stock but also enables smooth production processes and reduces costs through more efficient resource use.
In this article, we explore how a modern inventory management system enhances operations, minimizes downtime, and lays the foundation for future-focused business management.
What does an inventory management system do?
Inventory management systems are designed to monitor and manage stock and its movement from goods receipt to dispatch. Warehouse management systems, on the other hand, go further by controlling, monitoring, and optimizing complex distribution and storage processes.
Functions of a modern inventory management system
A modern inventory management system offers numerous features for increasing efficiency and optimizing inventory control. One of its core functions is real-time inventory tracking and control. With real-time tracking, companies can view current stock levels at any time, allowing them to make informed decisions about optimal reorder points. Automated processes, such as setting reorder points and automating reorders, help prevent over- or under-stocking, making overall inventory management more efficient. These tools ensure that optimal levels of materials, spare parts, and resources are always available, supporting smooth and continuous operations.
Types of inventory and their management
An inventory management system must efficiently handle various types of inventory to ensure seamless operations.
Asset inventory
Managing machines and equipment is essential for sustainable operations. An inventory management system helps monitor the condition and usage of assets to maximize their lifespan. With precise management, maintenance intervals can be optimized, and downtime minimized, which lowers operational costs and boosts productivity.
Spare and maintenance parts
Maintaining an adequate supply of spare and maintenance parts is a balancing act between cost-efficiency and operational readiness. An inventory management system plays a crucial role by ensuring that necessary spare parts are always available to minimize downtime. Through inventory control, companies can analyze consumption patterns, plan stock levels accordingly, and avoid unnecessary costs from overstocking. This approach makes the entire maintenance process more economical and reliable.
Technological developments in inventory management
Inventory management has come a long way from manual, paper-based processes to digitalization and automation. In the past, inventory was managed using physical lists and spreadsheets, which was time-consuming and prone to errors. Today’s digital inventory management systems allow for more accurate stock control through real-time data and automated processes. This enables companies to respond more quickly and flexibly to changes in inventory while minimizing human errors.
Modern inventory management systems can seamlessly integrate with other essential software solutions, such as ERP systems and CMMS (Computerized Maintenance Management Systems), to make inventory management even more comprehensive. A prime example is Elara’s software, which provides a central platform for integrating all inventory data, thus enhancing efficiency throughout the supply chain. By connecting these systems, data can flow freely, allowing all relevant information to be managed within a single system.
Elara and its inventory management features
Elara offers a comprehensive solution for real-time inventory management and mobile application capabilities that facilitate precise and accessible stock management. Companies can view current inventory levels at any time and trigger automatic orders as needed. This transparency helps prevent shortages and stabilizes production processes.
With Elara, the management of the entire inventory is consolidated in one central location, significantly simplifying communication between different departments and locations. The user-friendly interface enables even less tech-savvy employees to easily navigate the software and quickly find necessary information. Centralizing all inventory data noticeably enhances operational efficiency.
Automation and mobility in inventory management
Elara provides features for automated ordering and reordering processes that help reduce human errors and increase efficiency in inventory management. Companies can set threshold levels for stock, automatically triggering orders when these levels are reached. This ensures that sufficient quantities of materials are always available without requiring manual intervention.
With the Elara app, employees can manage inventory on the go—anytime and anywhere. The app includes features such as inventory scanning and real-time data access, allowing employees to quickly and effectively retrieve information and make decisions, whether they are in the warehouse or out in the field. This not only enhances flexibility but also boosts productivity across the entire inventory management system.
Elara’s conclusion
A modern inventory management system like Elara offers significant advantages in optimizing operations and increasing efficiency. The precise, automated, and interconnected management of inventory minimizes errors, reduces downtime, and ensures continuous production. Through integration with other systems, automation capabilities, and mobile access, Elara creates a comprehensive solution for today’s inventory management challenges.
Check out our success stories to learn how companies have successfully implemented Elara.
[In the age of AI, you never know if you’re reading something copy and pasted directly from ChatGPT, or if an actual human sat down to write this with some cool facts from their boss or operations team. That’s why we created a short and simple introduction to how we create content at Elara.]