The maintenance industry in Germany is grappling with an increasingly urgent issue: a shortage of skilled workers. Recent data from the VDMA (Verband Deutscher Maschinen- und Anlagenbau) reveals [...]
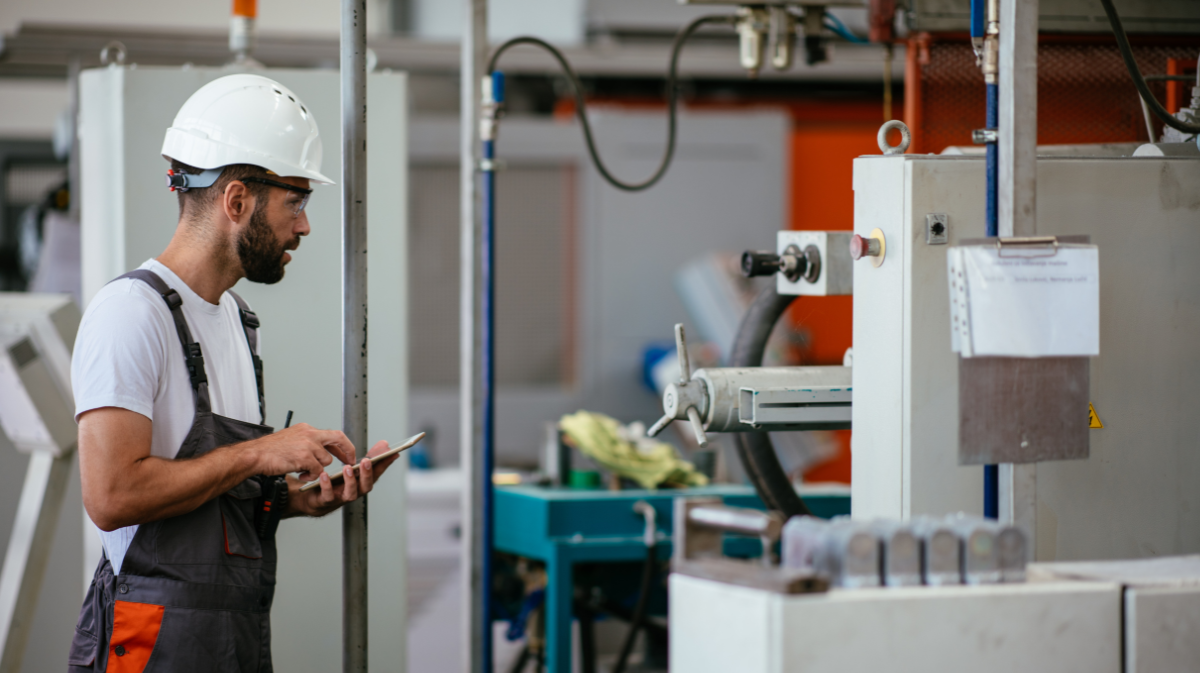
The maintenance industry in Germany is grappling with an increasingly urgent issue: a shortage of skilled workers. Recent data from the VDMA (Verband Deutscher Maschinen- und Anlagenbau) reveals that the number of vacancies for technical service technicians in maintenance and repair surged by 38% in 2022 compared to 2021, and by 8% compared to 2019. This trend underscores not only the escalating demand for qualified specialists but also the serious repercussions on the safety, efficiency, and longevity of systems and machines, which are essential to any productive economy.
The severity of this problem cannot be underestimated. A shortage of specialized maintenance personnel can result in costly breakdowns, inefficient operations, and even safety risks. Companies are struggling to recruit and retain qualified staff as demographic shifts and technological advancements continue to intensify.
In this article, we delve into the root causes of this skills shortage and explore potential solutions for the maintenance industry.
Demographic change and its impact on the world of work
Demographic change in Germany presents a fundamental challenge with direct implications for the labor market in technical professions, including maintenance. The country is facing an aging population, meaning a significant portion of the workforce will retire in the coming years. This trend is leading to a gradual decline in the available workforce and an imbalance between the supply of skilled workers and the industry’s demand.
In the maintenance sector, where technical expertise and experience are crucial, demographic change is intensifying existing challenges. There are fewer young people entering these professions, while the number of experienced specialists in active service is dwindling. This has resulted in a noticeable shortage of qualified workers today, and the situation is expected to worsen in the future.
Attractiveness of training occupations in maintenance compared to other sectors
The attractiveness of training occupations in maintenance is often overshadowed by other sectors. Although technical professions are highly regarded in Germany, specific aspects of maintenance can appear less appealing. Working in maintenance typically requires flexible hours, technical expertise, and the ability to work precisely under pressure. This contrasts with other professions that may offer a better work-life balance or are considered more prestigious.
Moreover, technical maintenance apprenticeships may not receive sufficient promotion or emphasis, especially compared to careers in the IT sector or other technology-oriented industries. This lack of promotion results in fewer applicants interested in training for maintenance roles. Despite its critical importance in ensuring production is future-proof, sustainable, and efficient, maintenance often receives insufficient attention.
Technological change and complexity
Technological change has fundamentally transformed the requirements of maintenance. Once primarily a manual activity, maintenance is now deeply influenced by technological advancements. Modern systems and machines are equipped with increasingly complex components that require advanced knowledge in areas such as electronics, IT, and automation. This evolution places high demands on maintenance specialists, who must possess not only mechanical skills but also in-depth technical expertise.
Despite these technological advances, there is a clear gap between the technical skills required and those available in the maintenance workforce. Many older professionals with extensive experience may lack the necessary knowledge of new digital and automated technologies. Meanwhile, younger generations who have grown up with these technologies may not always have the practical experience and understanding of the traditional mechanical aspects of maintenance.
Digitalization, automation, and the principles of Industry 4.0 play a crucial role in transforming maintenance. These technologies enable preventative maintenance systems that can detect potential problems early and minimize downtime. They also promote the integration of IoT (Internet of Things) devices and smart sensors, which provide real-time data to improve the efficiency of maintenance processes.
However, implementing these technologies requires adapting the workforce and its skills. Training and upskilling programs are essential to ensure that maintenance professionals are familiar with the latest technologies and can use them effectively.
Overall, technological change in maintenance presents both opportunities and challenges. The right strategies for coping with these changes are crucial for strengthening the competitiveness of German industry while ensuring the long-term availability of qualified specialists. This includes, for example, investing in training and lifelong learning to help employees continuously improve their skills and adapt to new technologies. Digital transformation through modern technologies and automation also optimizes processes and increases efficiency. Flexible working models such as flexible working hours increase the attractiveness of companies for qualified specialists. Innovative training programs and cooperation with educational institutions ensure that junior employees receive practical training and have the necessary qualifications.
Maintenance software to combat the shortage of skilled workers
Maintenance software plays a crucial role in addressing the skill shortage in maintenance. These software solutions offer a variety of features that help mitigate the loss of efficiency and expertise caused by the lack of skilled workers. Firstly, they enable better planning and organization of maintenance activities through automated workflows and schedules. This reduces manual tasks and optimizes resource utilization, which is especially important when fewer skilled workers are available.
Additionally, maintenance software promotes knowledge retention and transfer within the organization. By centrally storing maintenance histories, documentation, and work instructions, new employees can be trained more quickly. This is particularly helpful during times of skills shortage when companies may rely more heavily on less experienced or newly trained staff. Overall, maintenance software can help increase efficiency, reduce costs, and maintain business continuity even with a limited supply of skilled workers.
Elara’s perspective
At Elara, we’ve discovered that implementing modern maintenance software is instrumental in overcoming the challenges posed by a shortage of skilled labor. By leveraging preventive maintenance, our software enables customers to identify potential problems in properties early and act proactively. This significantly reduces unplanned downtime and allows maintenance teams to deploy their resources more effectively.
Additionally, the software’s central data storage and knowledge management capabilities support continuous knowledge transfer. New team members can quickly familiarize themselves with the system and benefit from the experience of their more seasoned colleagues, which is particularly crucial when the availability of experienced specialists is limited.
Overall, it is clear that maintenance software is a transformative force, not only in technical terms, but also in overcoming structural challenges such as the shortage of skilled workers. It helps to optimize operational processes while maintaining quality and reliability – a significant contribution to ensuring the competitiveness and long-term success of our customers in Germany and worldwide.
Find out what our customers have to say about Elara’s maintenance software.
[In the age of AI, you never know if you’re reading something copy and pasted directly from ChatGPT, or if an actual human sat down to write this with some cool facts from their boss or operations team. That’s why we created a short and simple introduction to how we create content at Elara.]